Thought I'd compile a build log on these, as they're nearly finished.
These are historically accurate replicas of the arrows found on the Mary Rose.
The shafts are hand-planed from European aspen into 1/2" diameter, 30.5" long. The arrows are tapered from 1/2" to 3/8" at the nock, and the taper starts 150mm from the head.
Once the shafts are planed (using a small wooden block plane and "chuting board") they are sanded and the nocks cut to accept a horn insert 2" long. The cut is made using a sharp pullsaw, which leaves a slot around 1/16" thick.

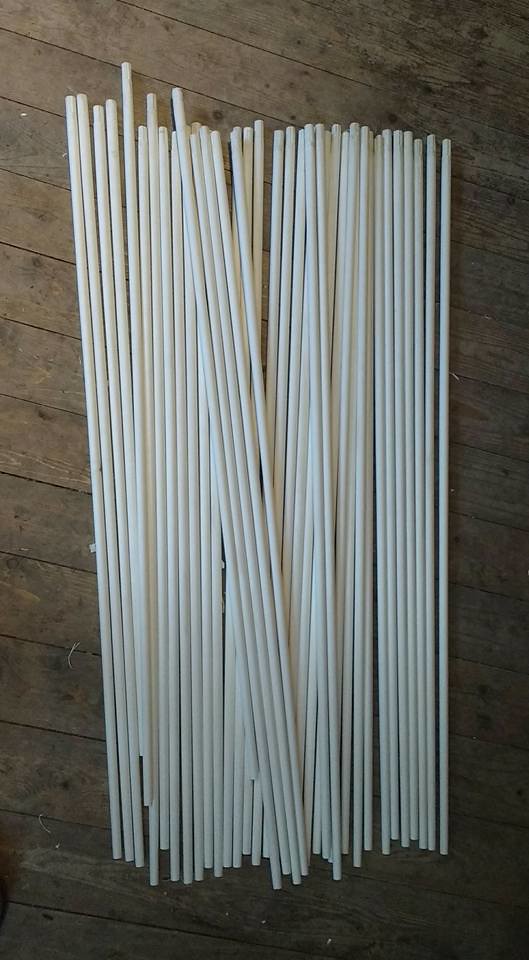
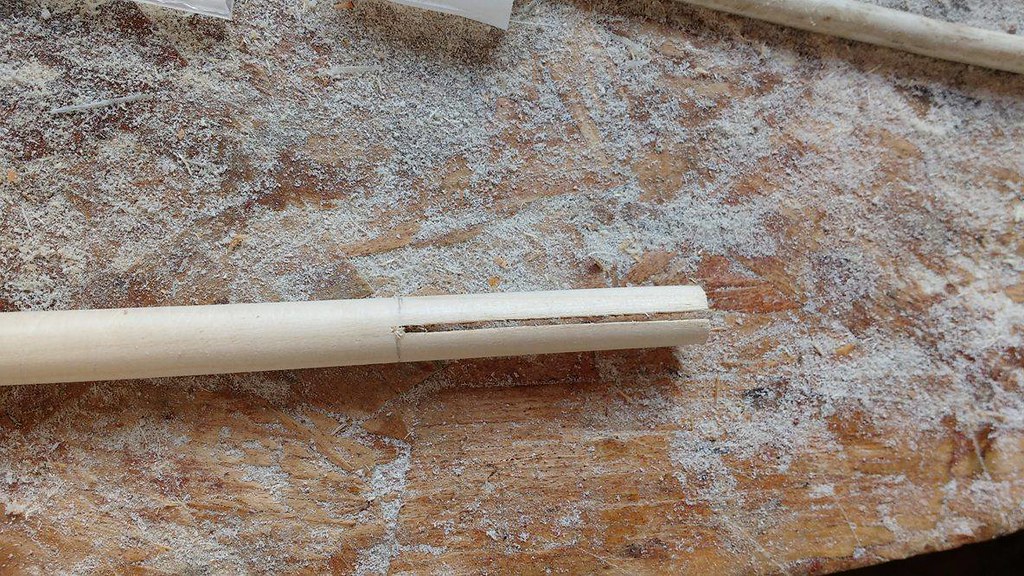
Cow horn is heated and flattened into sheets, and cut into strips. Each strip is then sanded down to 1/16" and glued in place using animal hide glue made from rawhide boiled in water and then sieved.
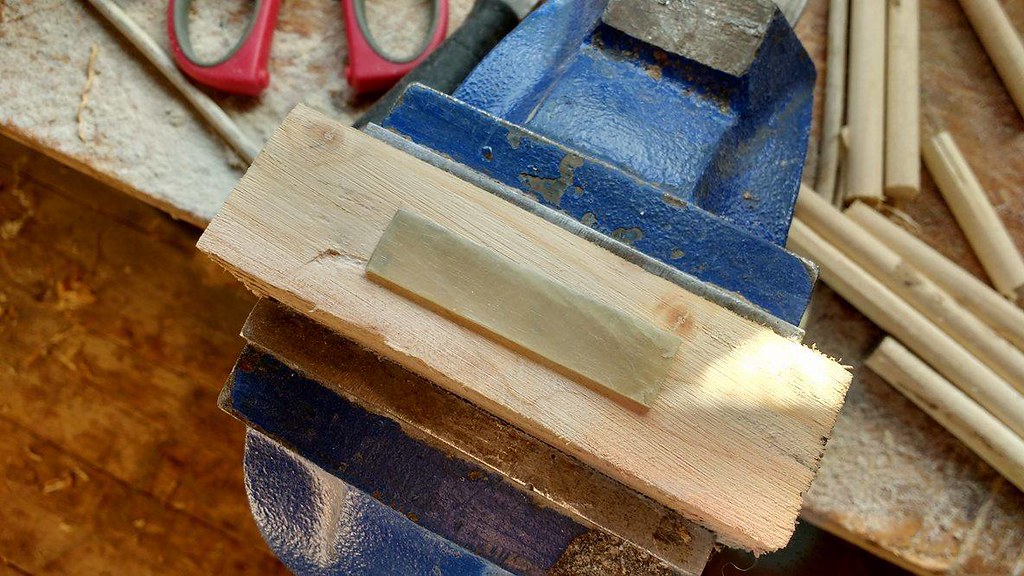
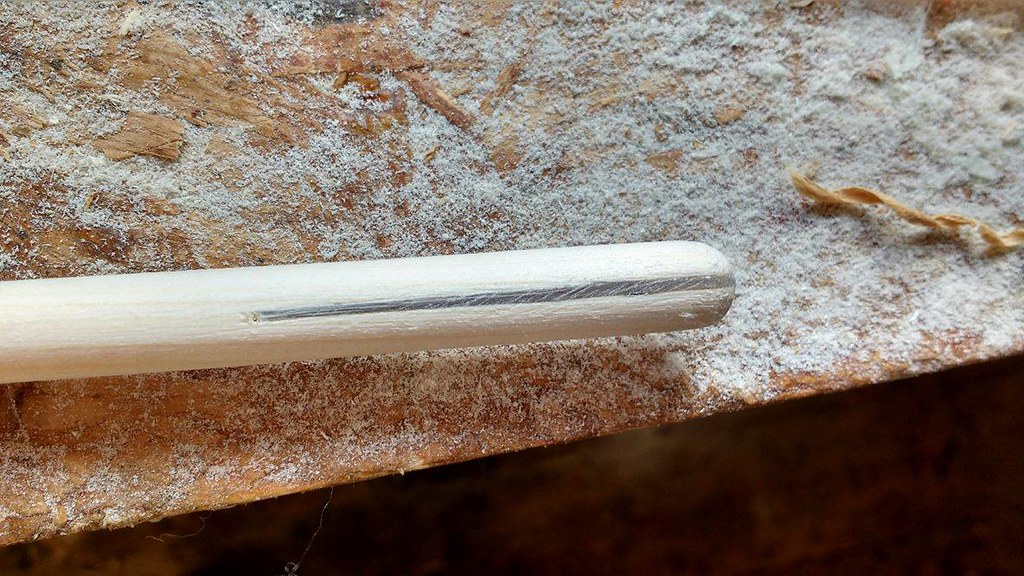
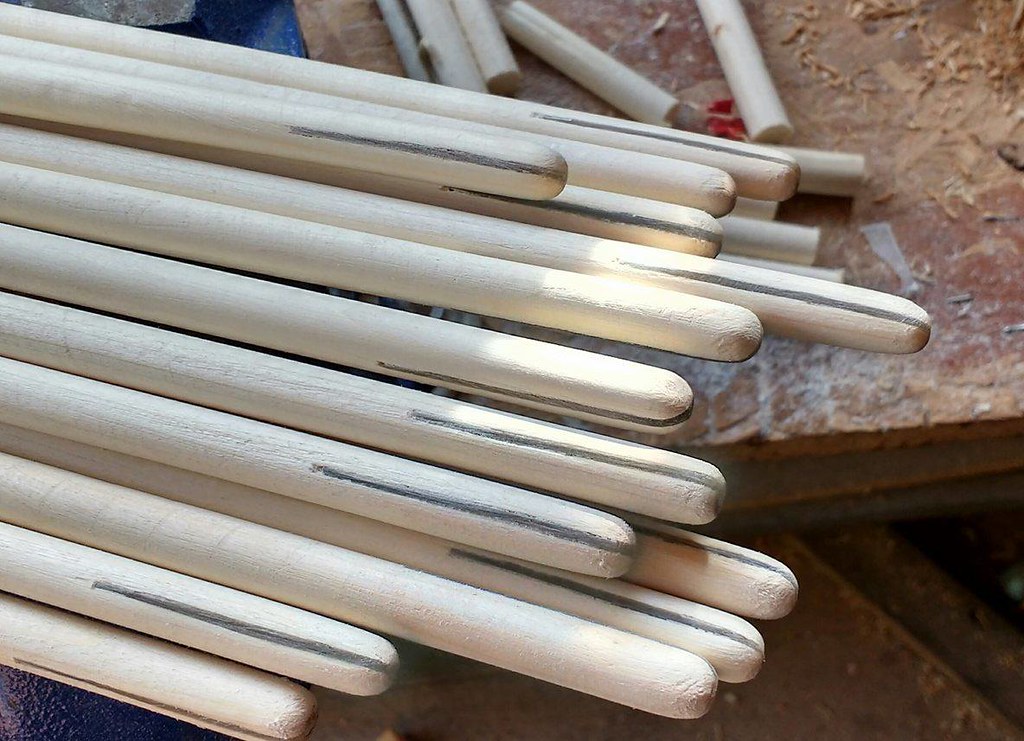
The feathers are goose primaries, and are split and ground until the quill is paper thin. They're glued to the shaft using the hide glue cooked down slightly to a thicker consistency so that it's more tacky and sets in about 5 seconds, making fletching very quick! Once the feathers are glued, they are trimmed to shape (7.5" long and 5/8" high)
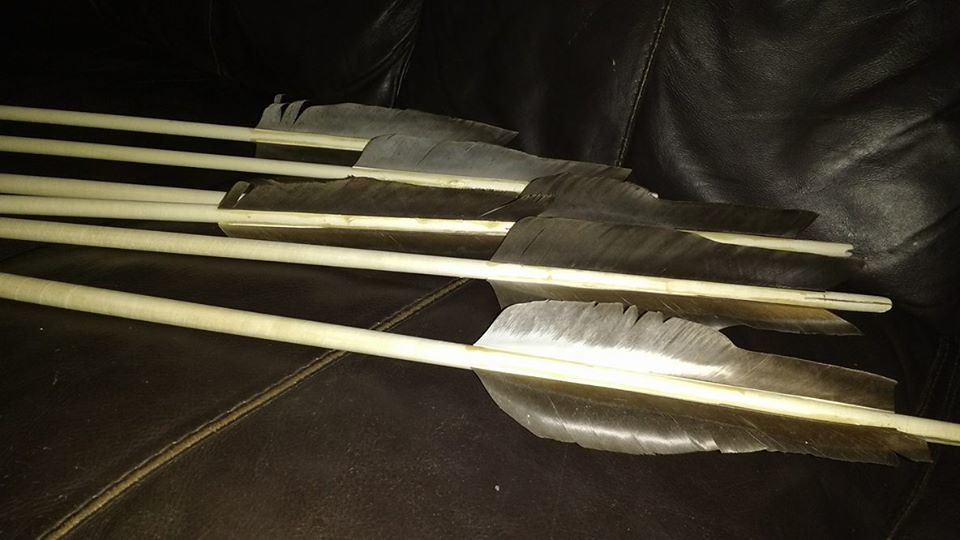
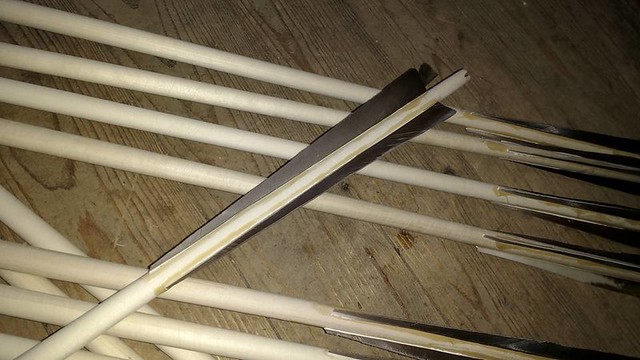
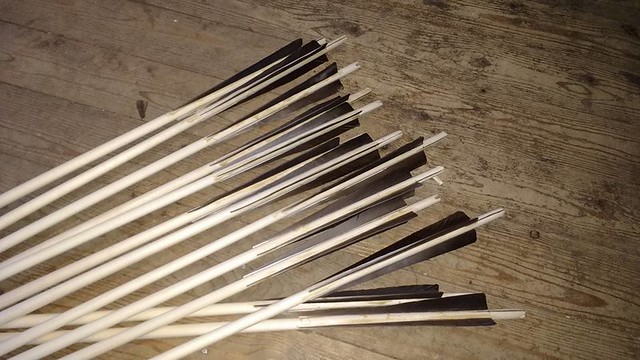
The hide glue isn't waterproof, so it needs to be protected using a wax and tallow compound mixture. The mixture is 50/50 and applied hot, as it sets the moment it cools. Once it's been applied roughly, a quick steam over some boiling water allows the wax/tallow mixture to run into all the cracks and cover any exposed hide glue, waterproofing it nicely.
Pure silk thread is used to bind the feathers for longevity, and is wrapped at around 6 turns per inch. It bites into the wax/tallow mixture which holds it in place as it's worked.
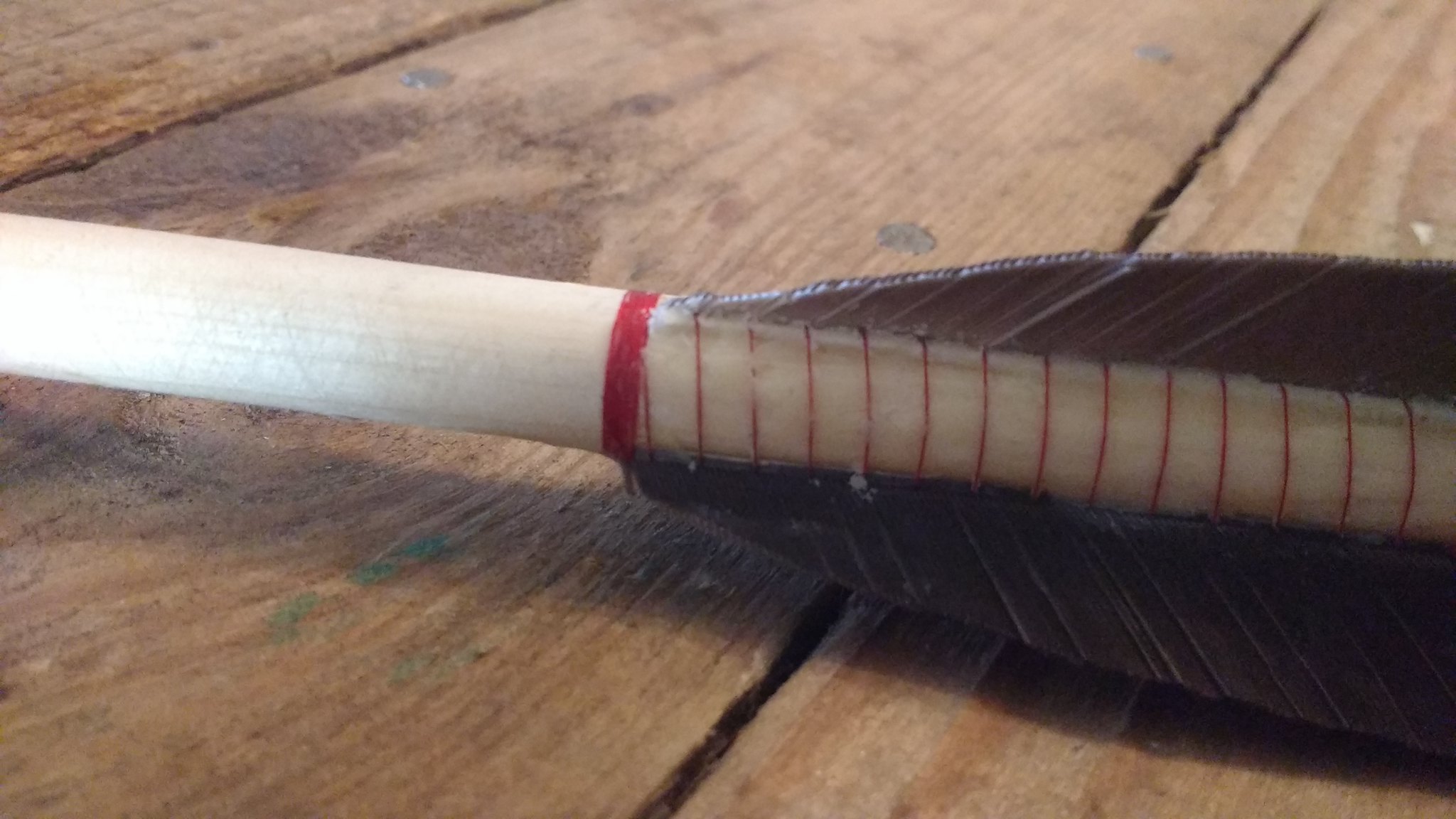
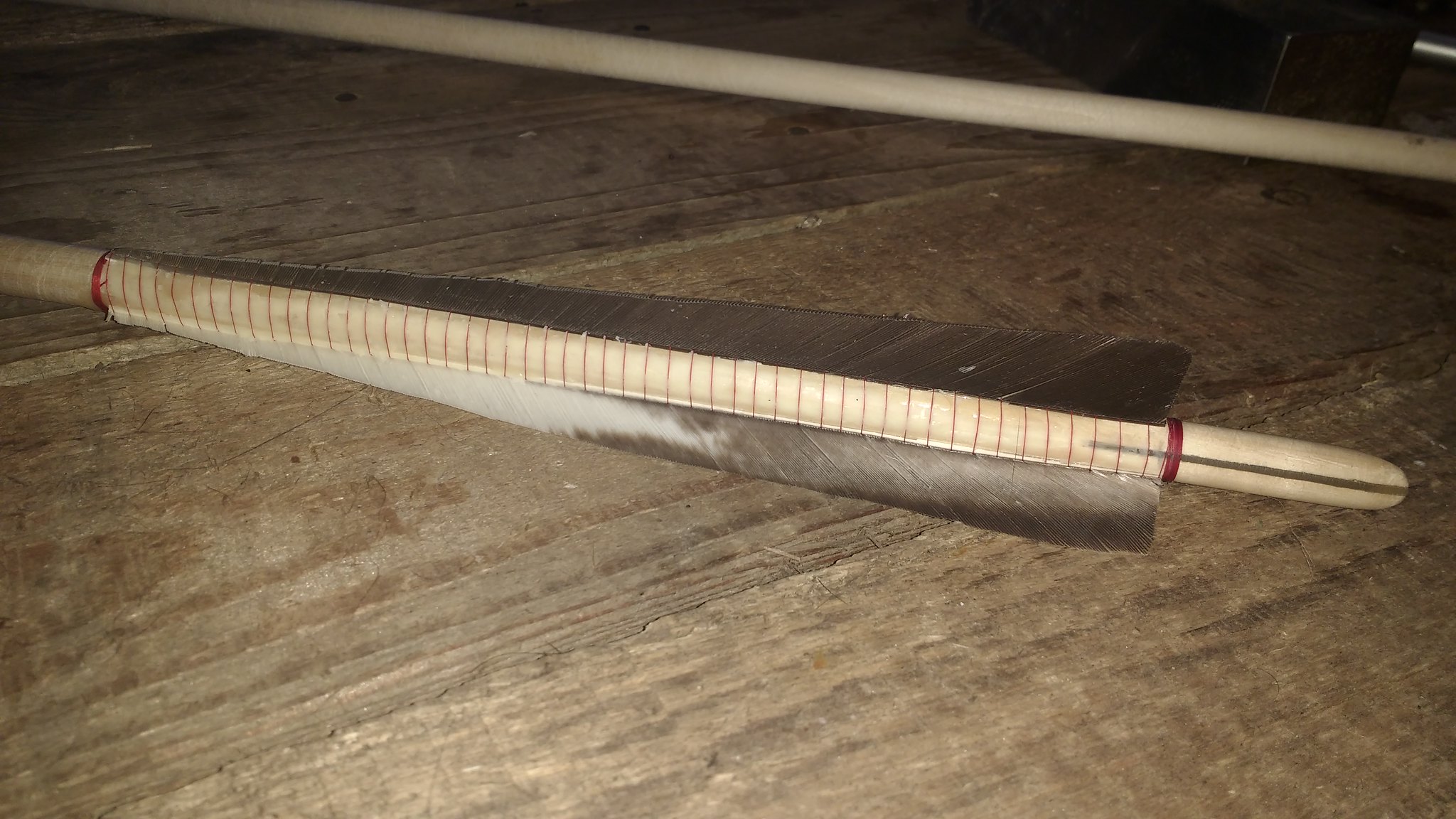
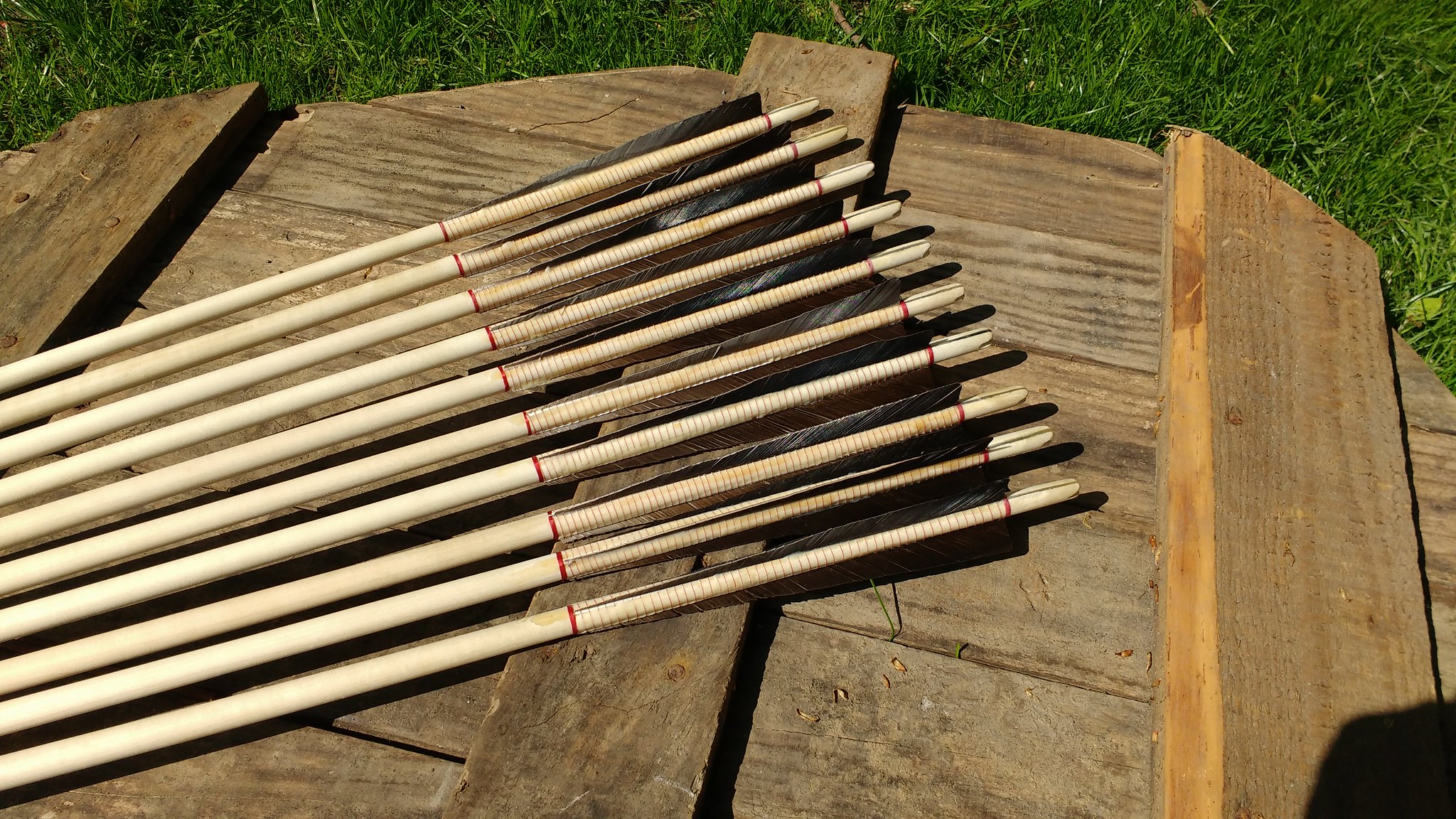
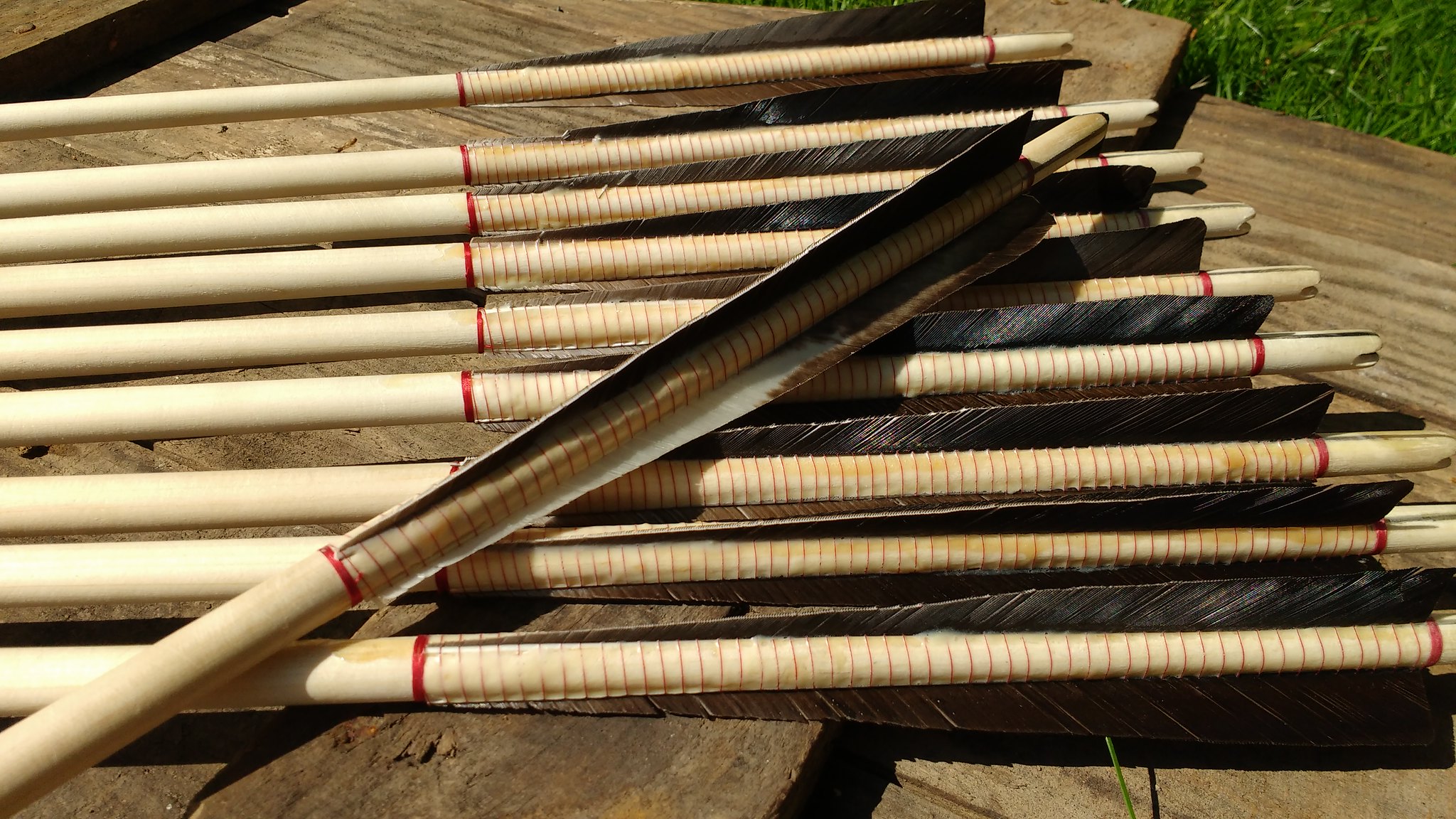
The final stage of the fletching is to cover the bindings in a verdigris compound. This is to secure the bindings firmly, provide a final waterproof coating for everything and the verdigris acts as an insecticide and fungicide to prevent things from eating the hide glue and feathers in storage. The mixture of the verdigris is done by eye, but it consists of lots of clarified pine resin heated gently until runny, mixed with some natural pine gum turpentine to make it a brush-able consistency, a shaving of pure beeswax to add plasticity and a good amount of verdigris powder, scraped from copper sheets suspended over red vinegar. The mixture is liquid over heat, and solidifies when cool. It's brushed on while still hot and left for a day or two to fully cure.
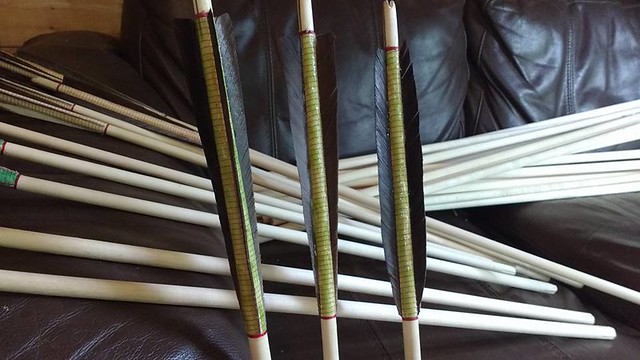
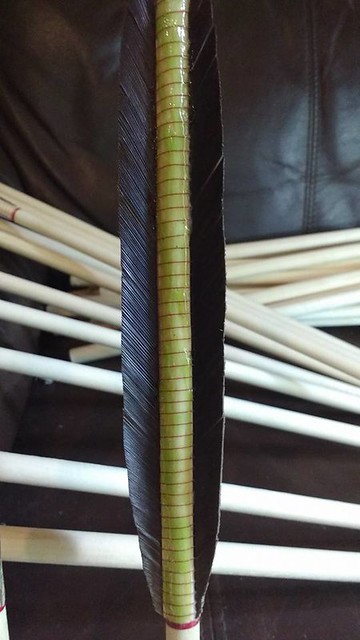
All that's left to do now is forge the heads, and I'll be making them based on a London Museum Tudor head find, which I'm currently in the process of getting more information about from the archaeology department. I'll update this once they're done.