Hiya,
I've lurked around this forum for a long time now. Theres LOTS of wonderful information about all sorts of subjects so hopefully I can add a tiny bit with my experiences this afternoon.
I'd recently got a loan of Bow Accessories by Volkmar Hubschmann and flicking thru the pages I spotted the details for the Oetzi quiver build.
This is a pic of the finished article from the book
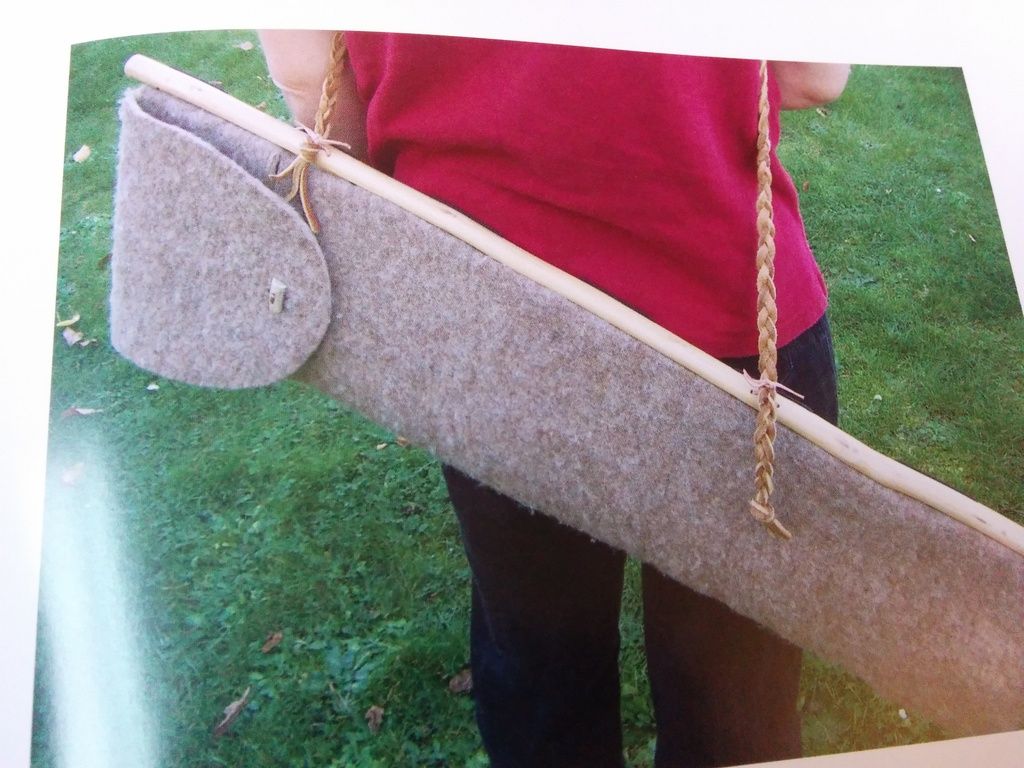
This was a style of quiver I'd seen somewhere before and really liked the look of. I have a 'normal' style of quiver which I have on a long loop over my shoulder, primitive style (since I mainly shoot field up in Scotland). This works fine but isn't particularly weather proof and too short so on occasion I get arrows falling out of it. Since the Oetzi style quiver is full arrow length it offers some protection from the rain and elements and is long enough to 'grab' the fletches and prevent them falling out.
Anyhow.
The build-a-long in the book has it made from felt! So I thought, "How hard can that be.....?"
I should add, my sister-in-law is a knitter/spinner/weaver in her spare time and she'd had some experience of felting before so she agreed to come and help. As a result, we deviated a bit from the instructions in that book which is why I thought I'd share what we did and what I might do differently next time, just in case anyone might want to give it a go.
Details.
The book suggested about 350g's of carded wool. There was a couple of options for they type of sheep's wool to use but I went for undyed merino. This was about £16 for 400g.
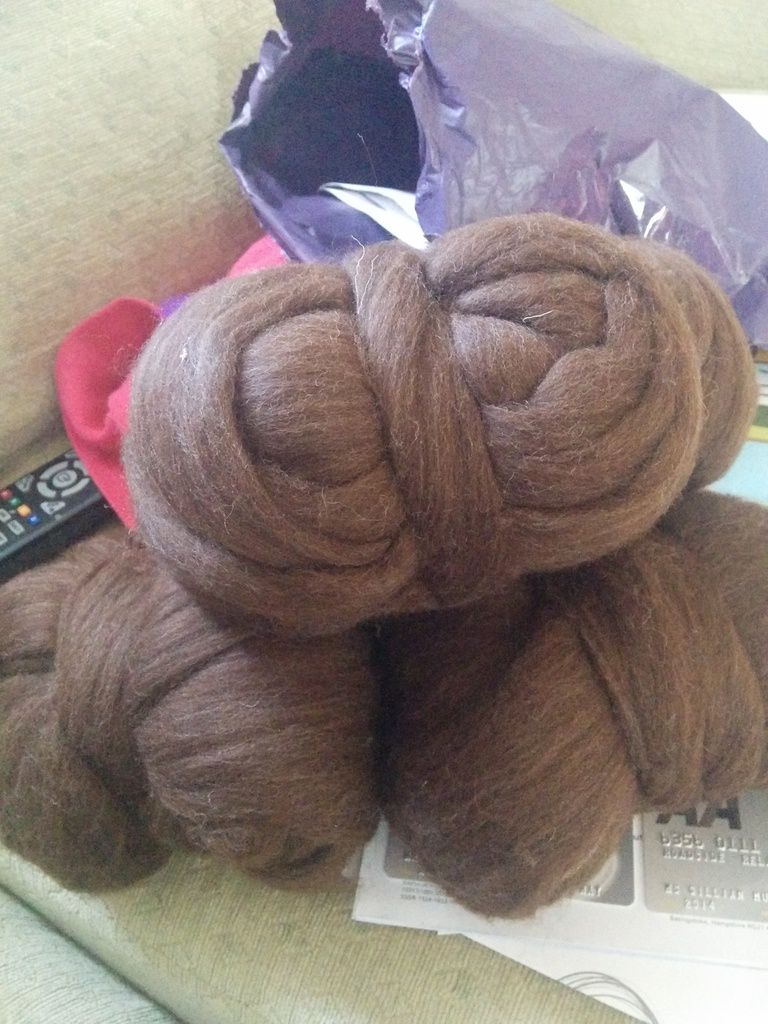
You also have to make a form of some sort. The dimensions the book suggests are 110cm x 33cm (at the wider end) and 24cm at the narrow, bottom end. The only thing I had to hand to do this was cardboard and some plastic bags, sealed up with duct tape.
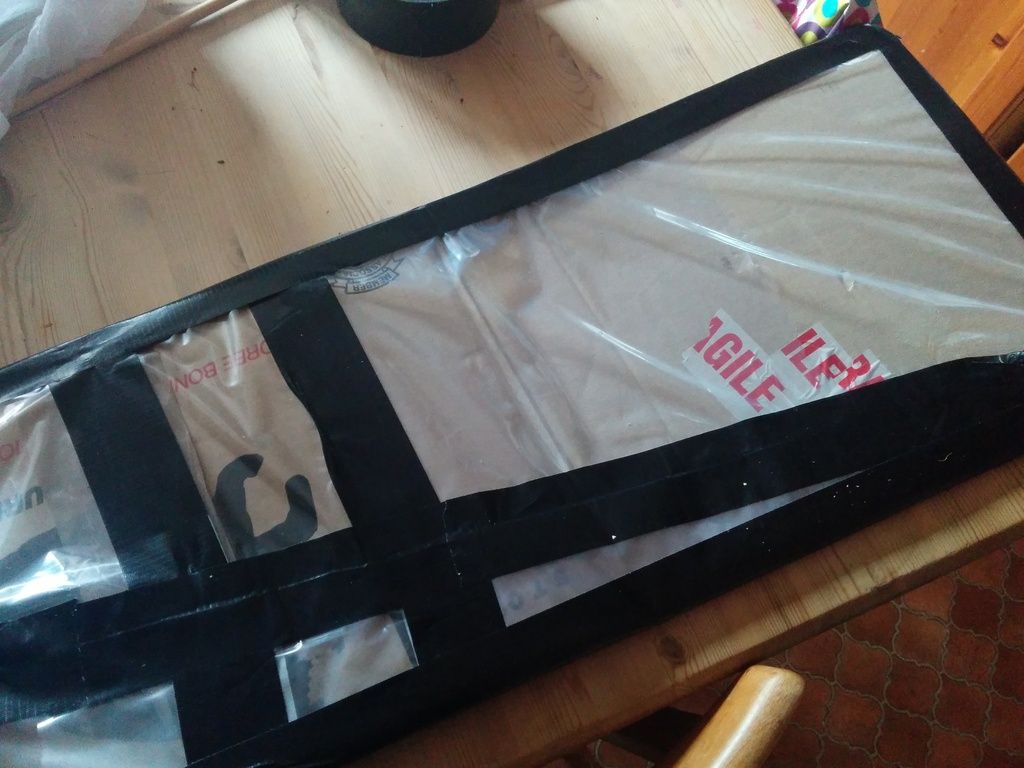
The reason for the large size is that it'll shrink about 1/3 once it's felted but certainly it looked like a bit of a monster to start with!
The other things that we used/needed were some towels, a big sheet of bubble wrap, soap (the more 'pure soap the better apparently. The book suggests olive soap. Again, didn't have any so ended up using some handmade simple soap). and hot water. And time.
First thing to do was separate the wool out and wrap it round the form. It was fine to do this is smaller pieces, like 12" lengths, just try and wrap it evenly with no lumps and making sure that they were overlapped a bit. We also made sure that they wrapped around the edges rather than the end of a piece finishing at the edge of the form.
Wool was laid over the form in both directions, width-wise and length-wise. We also put an extra layer over the bottom so it would be slightly thicker and a bit harder wearing.
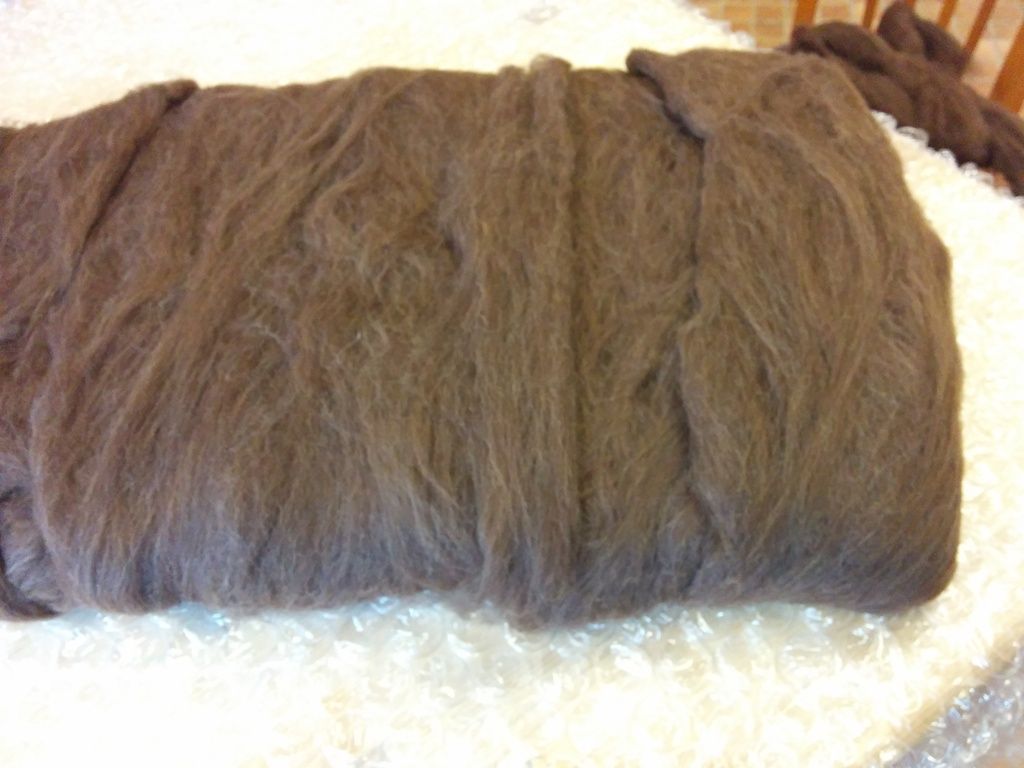
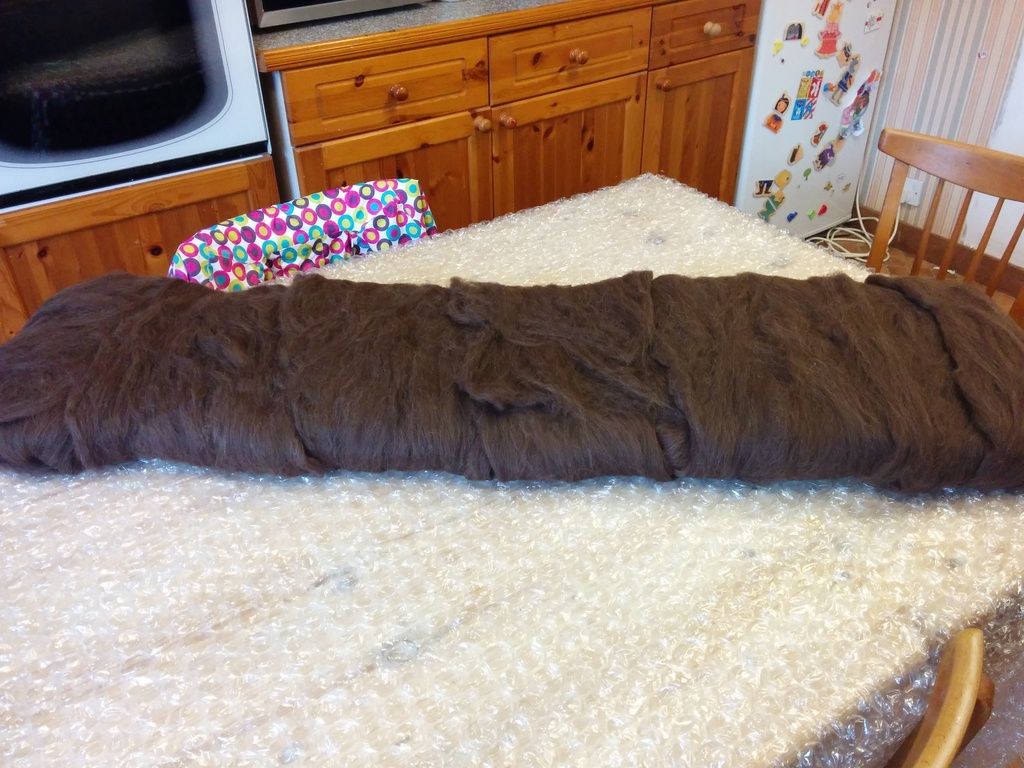
Next you sprinkle hot very soapy water over the wool and start to gently pat it down so it flattens and gets wetter. The soap is so the fibres don't stick to your hands and it's easier to rub over the surface.
At this point, it's worth noting that that was partly the reason for the bubble wrap. It holds the water to the underside of the piece so while you're working the top side, the underside gets a little worked too.
Once it's wet you can really start to put a bit of pressure on it and keep rubbing it backwards and forwards. Again the reason for the bubble wrap. We folded it over the top of the quiver, added a little more soap and water and rubbed up and down over this . The bubbles act a bit like lots of little points of contact with the surface of the work which (apparently) speeds up the process a bit.
We worked one side for 10 mins or so then flipped it over and worked the other side for about the same, paying attention to the edges and trying to keep it fairly even.
About half an hour of this it was looking like this:
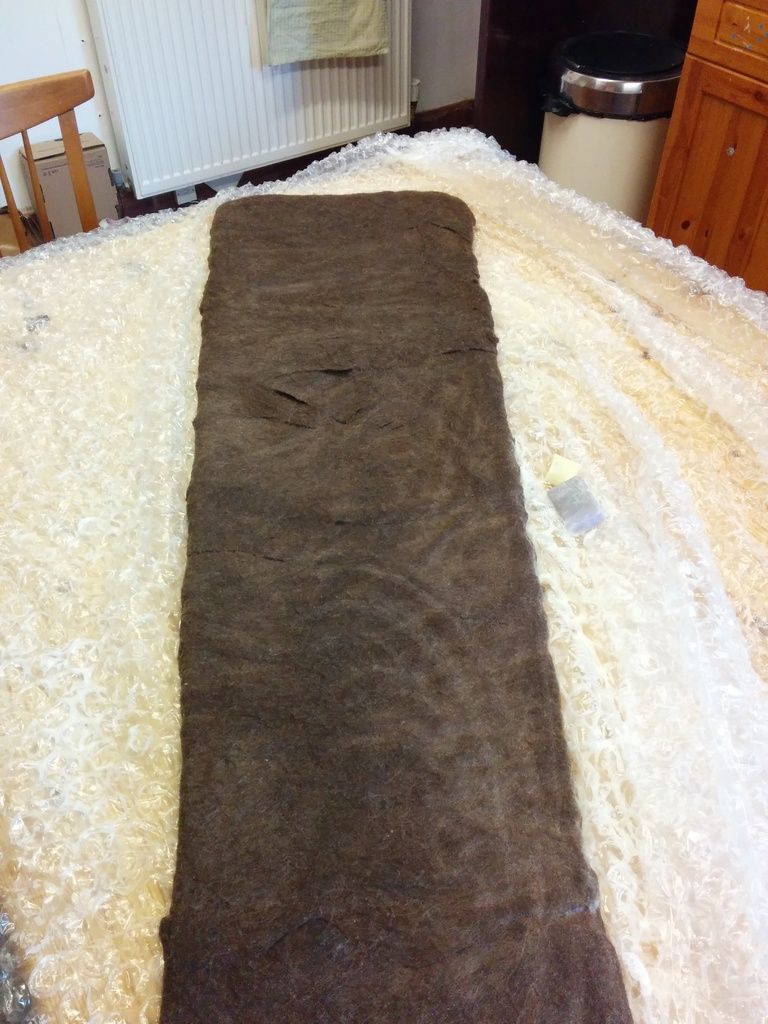
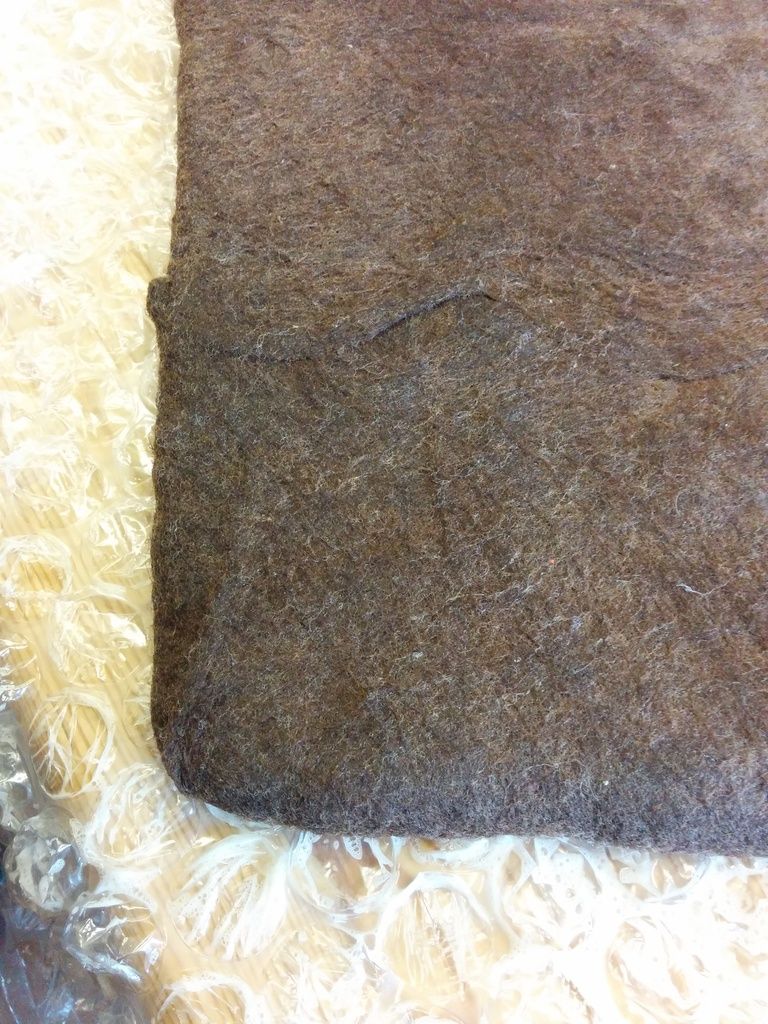
At this point I cut about 15cm down from the top right across the front and up the sides to make a flap and to be able to remove the form from the inside.
It was at this point we differed quite a bit from the book so I'll detail what we did.
Once the form was removed, we put in some plastic bags inside then washed it in a shallow bath of hot water to help get the soap out. We then rinsed it in a cold sink of water and repeated a couple of times.
Once done, and with the plastic still inside, we put it in the washing machine at a 60 degree wash, without any soap powder or anything, for about half an hour.
In retrospect, it was a little silly as the bags bunched up in portions of the quiver so some sections of it fulled (or shrank) more than some other bits!!!!!!!
But it was shrinking!!!. I removed the bags, pulled/stretched the more shrunken bits out a little and stuck it back in the wash, again at 60 for about another 20 mins.

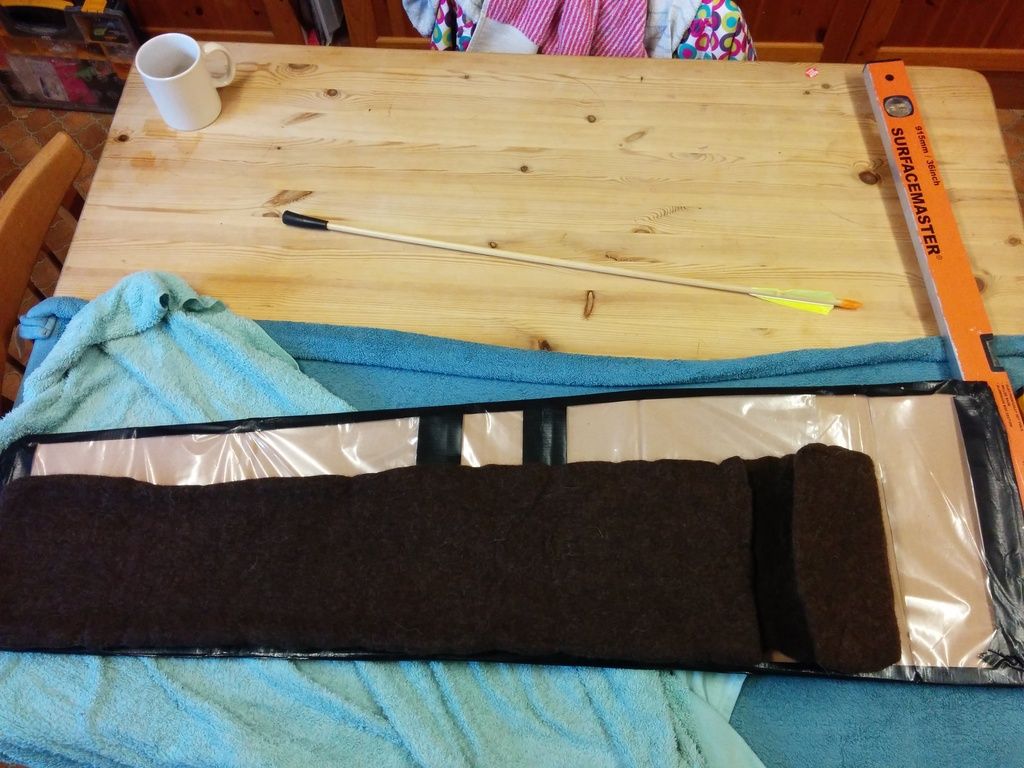
This is how it looked when it came out again after this. Better, but still a bit uneven at the edge.
In the book, it describes doing the fulling process by rolling it in a towel. Fulling means to compress and better pack the fibres together creating a denser felt.
Since the length was only a tiny bit longer (and this could be cut down to fit anyway) I concentrated on trying to reduce the width and even out that annoying edge.
I rolled the quiver along it's length in a towel, really quite tightly then rolled it back and forward with quite a bit of pressure, paying particular attention to the wider bits and not so much on the narrower section. I periodically flipped it over and rolled the other side too.
I did this for about 15 mins or so but by then it was getting quite dry so I wonder that there would be limited effect. I also stuck a straight edge down inside it and sort of bashed the lower points out a bit which also seemed to help.
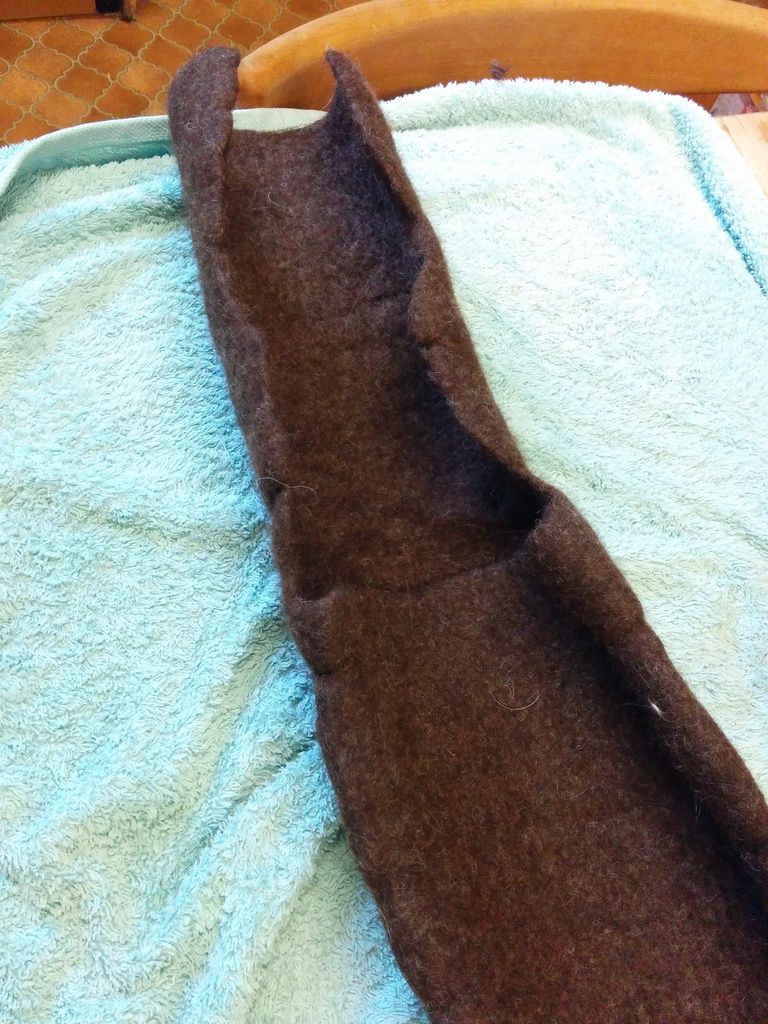
Once it was almost dry, flattened out I then turned it inside out. The edges were slightly lumpy so turning them inside hid them and made the edge appear a bit smoother.

So this is where I'm up to so far. I've not got a hazel stick or anything to act as a strap as yet. I'm going to let it dry for a few days and see how it settles. I think I can wet any lumpy/uneven bits and smooth it out again.
On the whole tho I'm pretty chuffed!! It worked way better than I thought it might and was a little easier with the washing machine method than the suggested hours of fulling by hand that the book suggests. Yes, I suspect you'd get a much more even finished doing it fully by hand but as a first attempt on what I had earmarked as being a bit of a "Such it and see, how difficult can it be?/trial attempt".
I'm also quite surprised at how solid it's become! it's going to be a pretty robust quiver once finished. Maybe not quite as slimline and refined as the one in the book but definitely "primitive" or rustic! hehe.
I'll post up some more pictures when I get it finished.
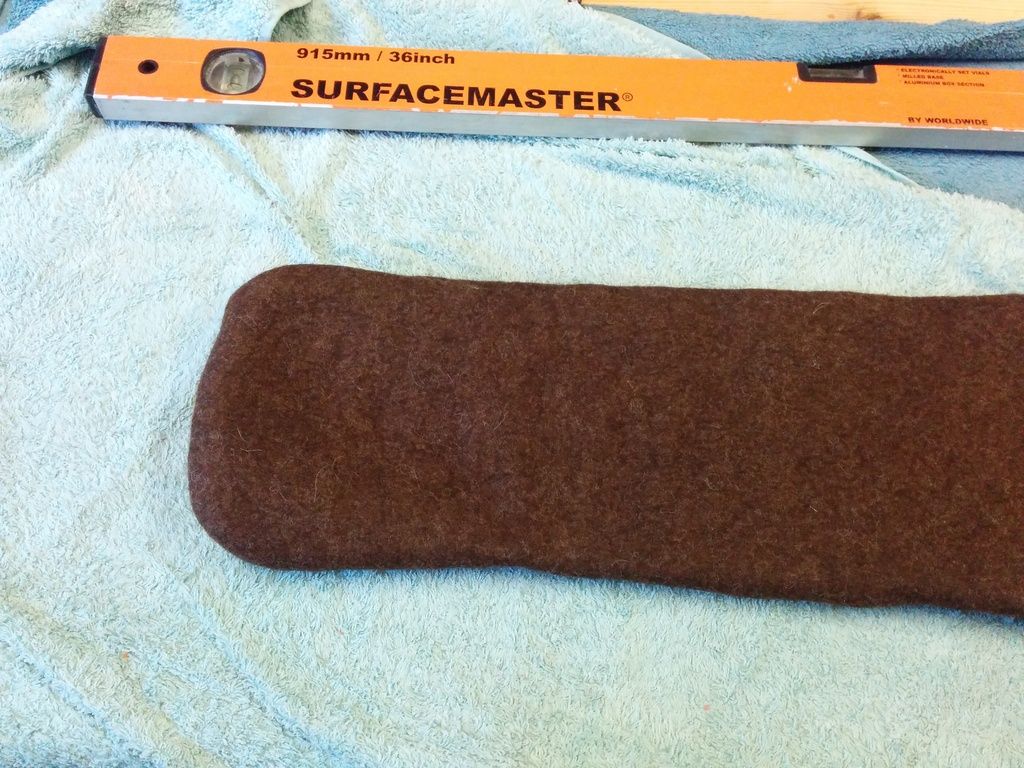
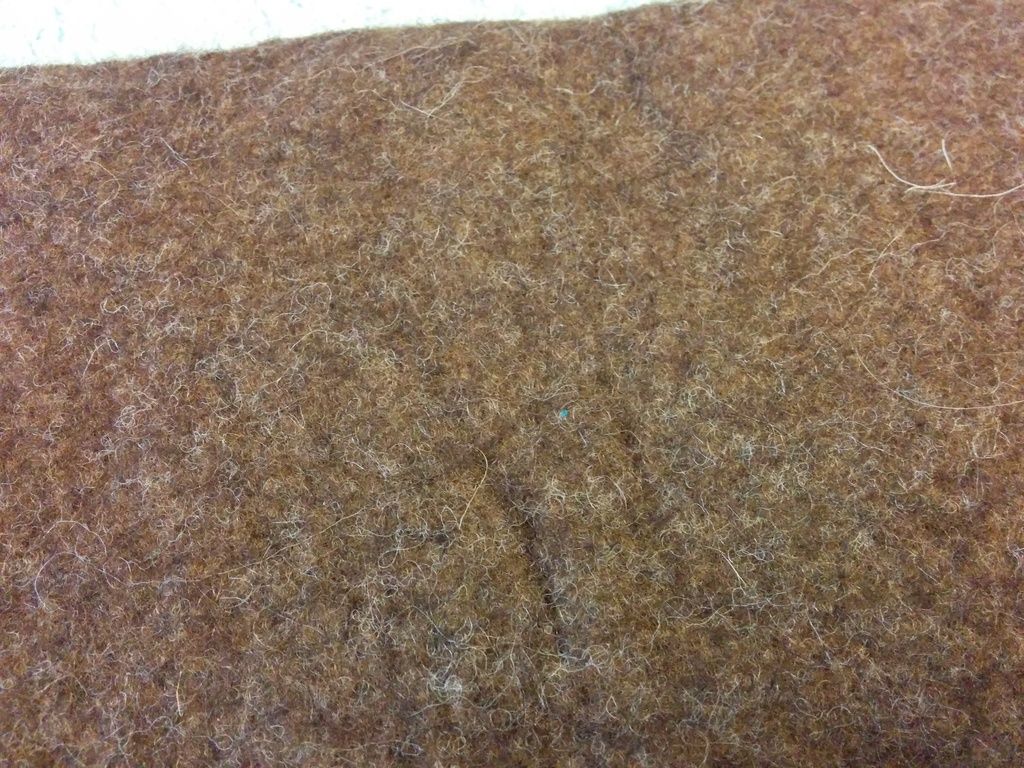
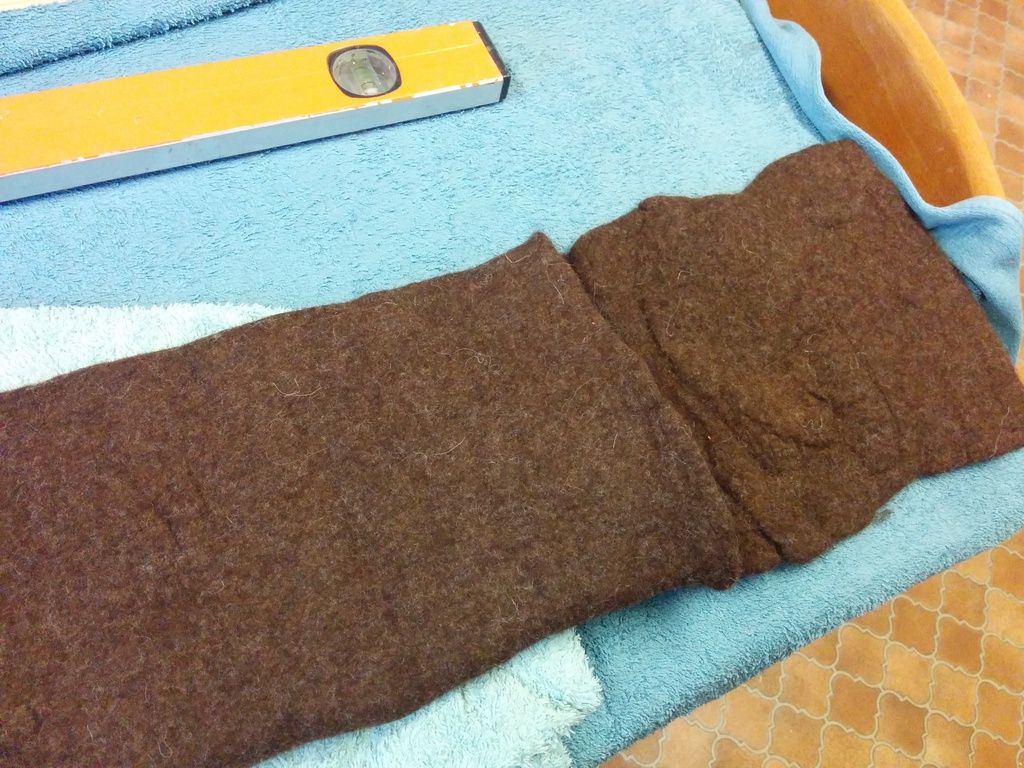