I had a corn fed eastern South Dakota doe given to me in late December and I finally got her thawed out enough to process. She had almost an inch of fat on her back over her hips. Dang!
I collected almost 7 lbs of pure tallow from her and rendered it down slowly in the oven. I had always wanted to try soap making, and this was the perfect opportunity. I spent several hours online researching soap making basics before I searched for deer tallow soap recipes. Turns out I am not the first duck in the water on this!
Hang on folks, there are a few photos to follow, but I am not turning this into a soap making lesson. I strongly recommend you spend the time I did researching, it is not hard to do, but there are some very fine details I recommend you learn about before you start on this wonderful skill!
Step one is mixing the pure lye granules with ice cold distilled water. You want water that has no hardness, no minerals apparently. Measurement of the lye depends on the strength of the lye and the fat profile of the other half of your recipe. You do NOT go by guess and by gosh!
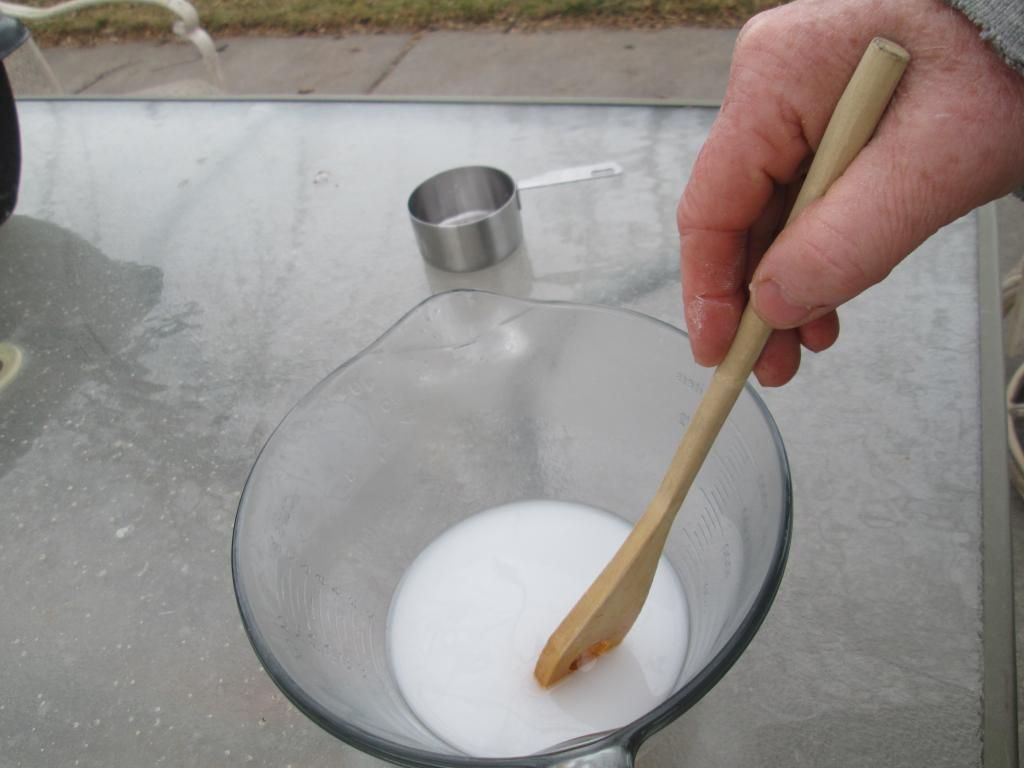
Next I measured out the exact weight in rendered tallow, that's the dark liquid in the larger mixing bowl. I had to cool the lye solution to 125 degrees to match the temp of the rendered and liquid fat. I cheated and used 10% canola oil, since it supposedly improves the lather of the finished soap.
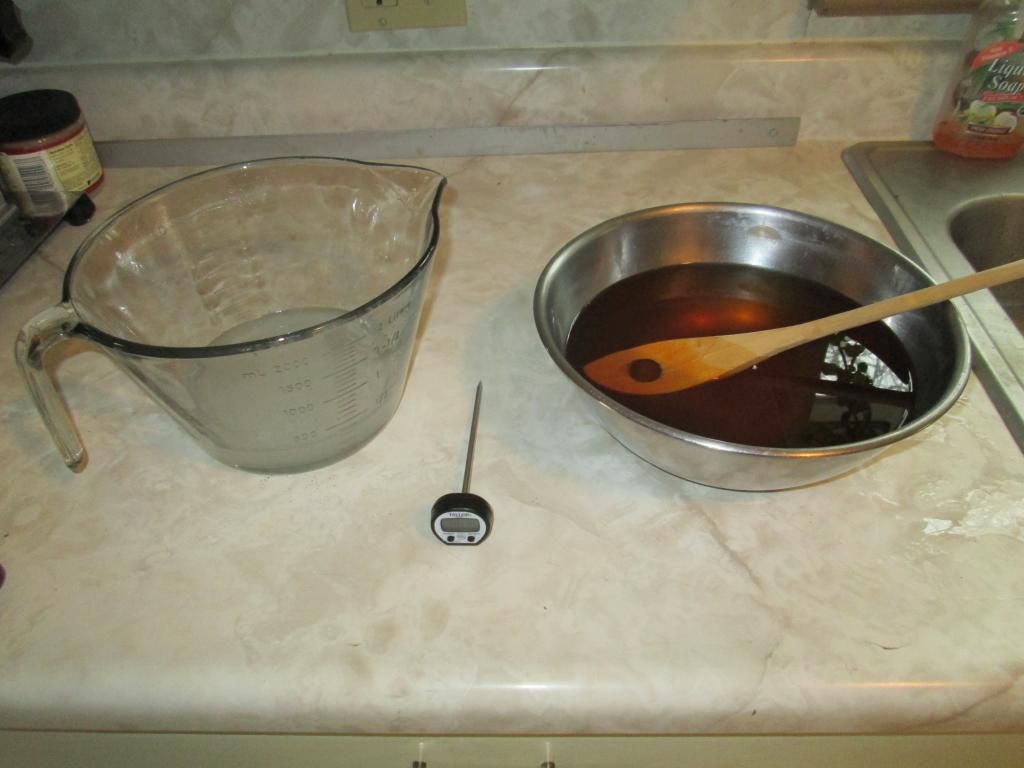
The lye solution is VERY slowly dribbled into the warm fat, stirring constantly. You are mixing water and oil. Easy peasy, right? Wrong, temps have to match perfectly, you cannot add too much water too fast, and you cannot add the fat to the lye, the lye must be added to the fat. Well, here I am stirring the pot! And stirring and stirring and stirring.
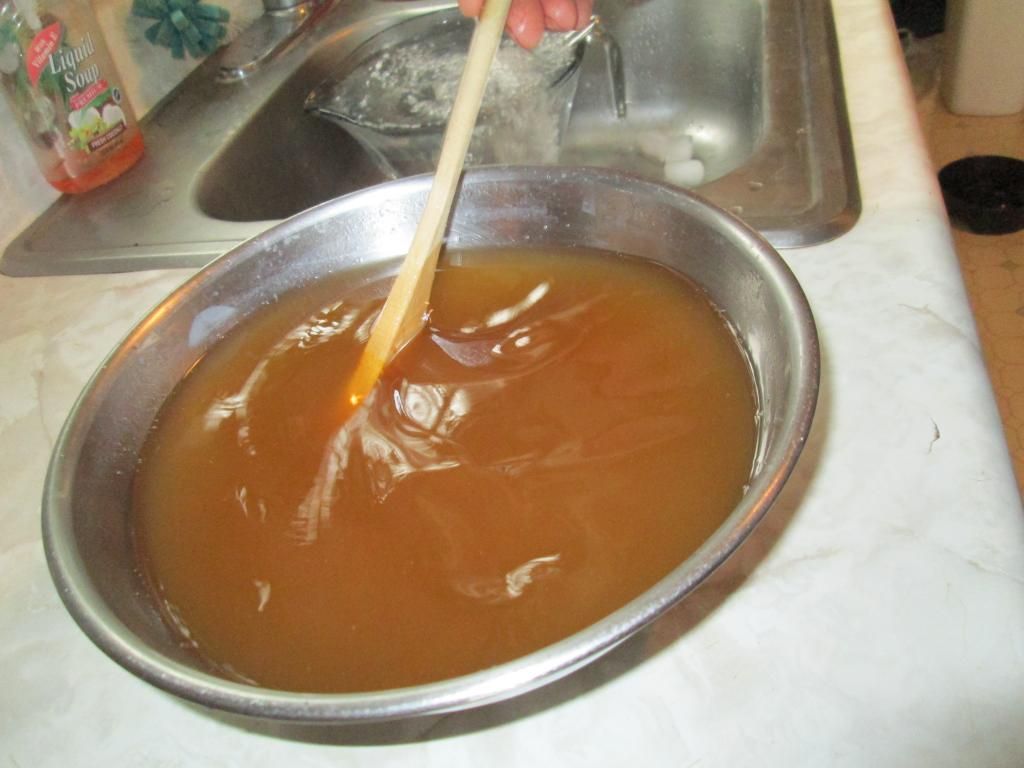
You stir for quite some time with absolutely nothing going on. You just stir. Stir some more, and you are still stirring. I went stir crazy. But then it started to turn color, losing the clear amber color and turning to something that reminded me of nothing so much as good roast chicken gravy!
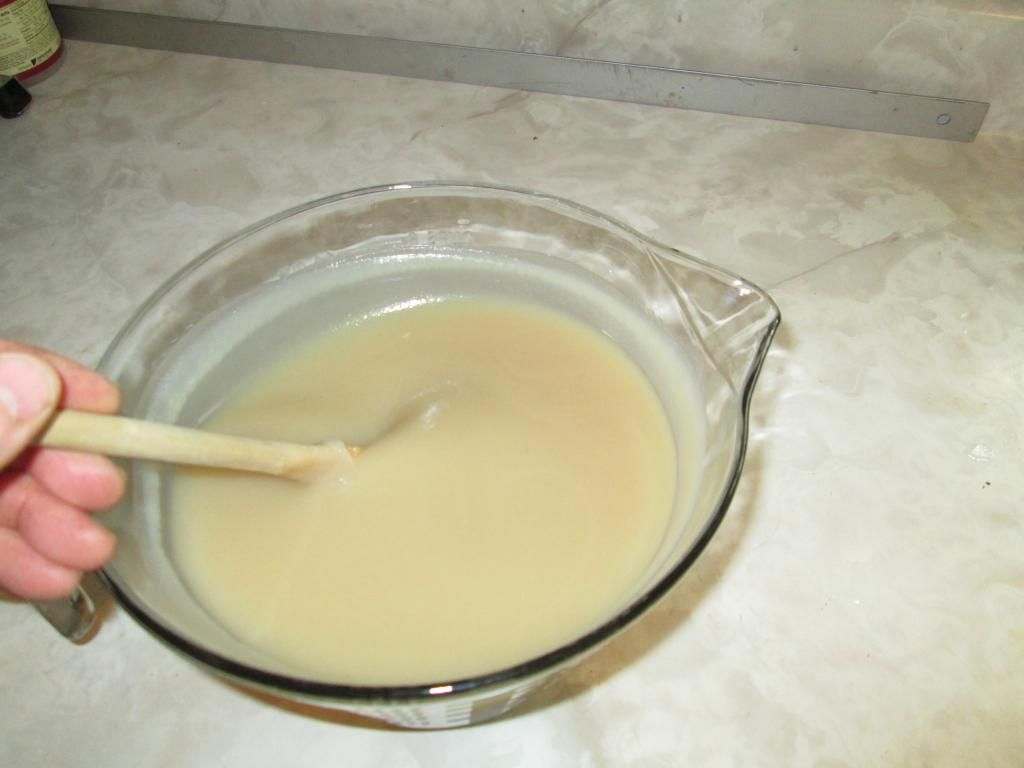
It starts to thicken a little too, like making gravy. And still you keep stirring.
And now here is where you are about ready to stop stirring. The stuff is becoming thicker and thicker until you get "trace". Trace is the soap maker's technical term for when the stuff gets so thick that it leaves a trace when you pick up the spoon and what drops back in the pot leaves a trace of it's shape. I found out today that I stopped a bit too soon, I shoulda...you guessed it...kept stirring.
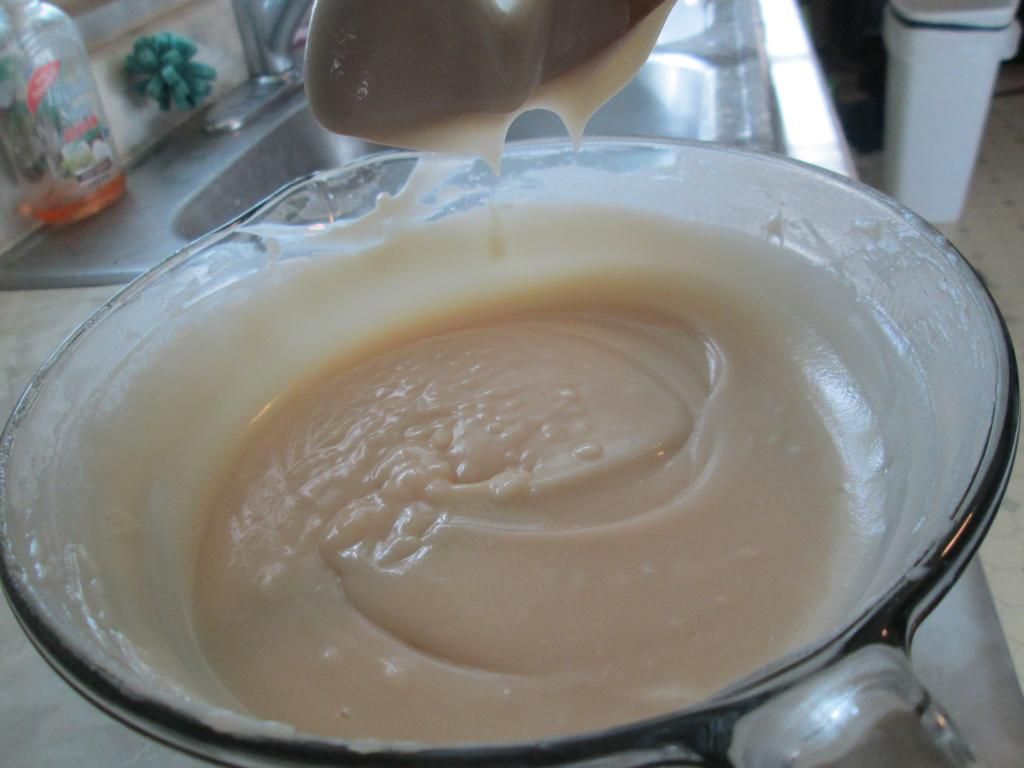
I then turned the mixture into a shallow and wide plastic storage container and wrapped the whole thing in heavy bath towels. You want it to cool very slowly now. It has begun to "work" and the lye is saponifying the fats. At this point, the fats and the water should not separate....if you did a good job stirring! I cut the raw soap into blocks so that more air gets to more surface area, this allows the soap to finish curing faster. Couple weeks and I have a batch of nice lye soap!
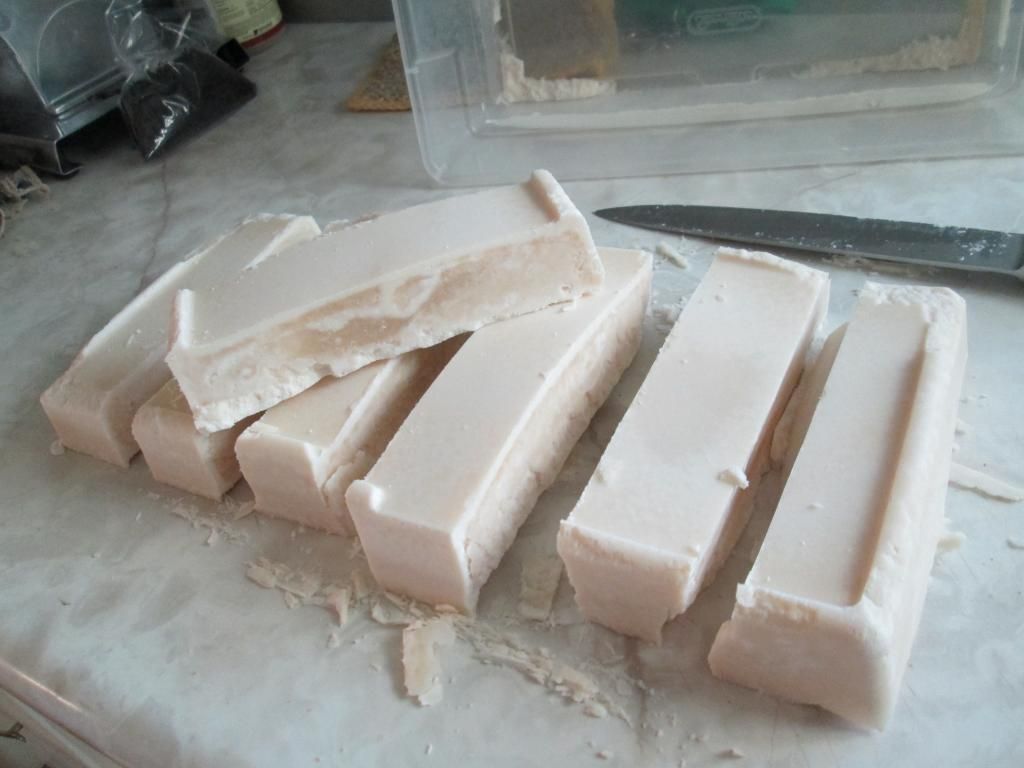