I’ve made previous router type shaft makers using various woods for the “block” that goes over the router bit and holds the shaft against it. The holes for the shaft in them wore out too quickly. Here’s the latest one which uses a 3/8” pipe tee for the “block” which is fitted with drilled-out fittings as bushings on two of the ends for making 5/16” and under diameter shafts:
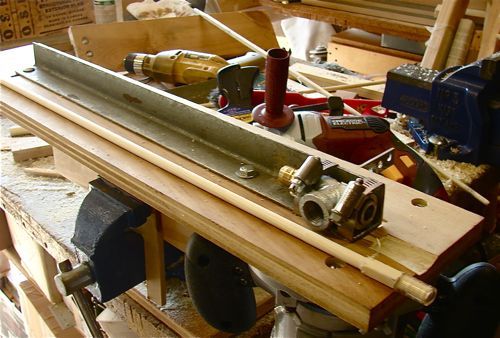
For those that aren't familiar with router type shaft makers, here’s some good threads:
http://www.primitivearcher.com/smf/index.php/topic,43769.0.htmlhttp://www.primitivearcher.com/smf/index.php/topic,41232.0.htmlI really like asharrow’s rig in the threads above and copied it in a much cruder fashion. His uses an aluminum block and drilled out bolts for bushings. Alas, I’ve no access to a machine shop which I think is needed for making the holes in the bushing concentric enough- so I cobbled together this rig.
The angle brace attached to the far side of the base board in the pic above holds a dial indicator. Like Asharrow said in the first thread above, it really helps with adjusting the cutting depth of the router bit. It’s taken off after getting the rig set up tho'- the vibration from making shafts isn’t good for the indicator, i.e. the end fitting on the indicator is now lost in a ton of trash on the shop floor

.
A brass fitting is used on the out-feed end. The fittings shown below have differing hole diameters which yield 0.313, 0.305 and 0.295 shafts. I selected fittings which had preexisting concentric holes or factory machining inside them (like the plugs). That helps ensure concentricity is maintained when drilling and enlarging the holes.
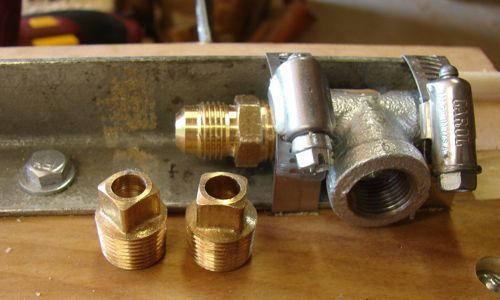
The different sized holes are made by first gingerly drilling out the fittings with a 19/64” drill bit then enlarging the hole using an ~5/16”reject arrow shaft or dowel, oil and some 280 loose grit. Coat most of the the dowel or shaft with oil then the grit. Chuck the dowel into a drill and run it back and forth through the drilled hole. Repeat as needed with more dowels or shafts until the hole is the desired right size. This method It also smooths out the gouges left by drilling the hole.
The infeed end is a cast iron pipe plug drilled out to, I think, 27/64" and then with the square head of the plug sawn off. No need to finesse the inside of it like the out-feed fitting.
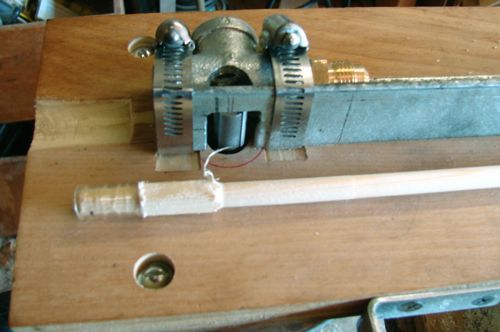
Wood is ripped into roughly 0.32” squares with a bandsaw. This thinness permits making two shaft blanks from 3/4” thick wood or 4 from 1-1/2” thick wood. The blanks in the photos were ripped from a big box store “white wood” 2x4.
To chuck the shaft blank into a drill, one end of the blank is slowly hand fed and rotated into the shaft maker. This makes a roughly rounded end over which a short piece of 7/16” OD x 5/16” ID vinyl tubing is fitted. This works well for chucking into a variable speed 1/2” drill. A 12 point socket doesn't work- the soft wood strips out. toomanyknots wooden thing pictured in the first post above would work tho'.
The only downside to the rig is that the blanks need to be at least 4” longer than the desired shaft length. Most of this excess length is because the portions of the bushings that actually contact the blank and shaft are kind of far apart. That leaves a fair length of both ends unburnished and the first end fed through is a tad too small in diameter and has a rough finish. Asharrow’s rig would greatly reduce this. The smaller diameter rough end won’t matter if it’ll be the nock end and it is aft tapered to 9/32” or 1/4". Here’s poor pics of the ends of a shaft:
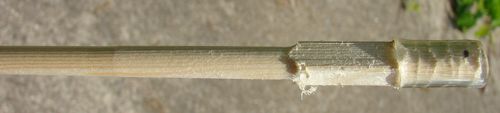
