Thanks, George. This kind of enthusiasm makes it all worthwhile, and keeps me doing creating this thread.
This morning, I made a crossbow string. I am the WORST string maker ever, meaning although they are perfectly safe and functional, they are not pretty. There are many, many ways to go about making a crossbow string, from a mega-authentic hemp one, to using modern materials and serving the ends in different ways. This is my lame way, so please don't laugh. I will say I need to really practice and get better at making nice looking strings.
I made up a jig out of scrap red oak and some bits and pieces of hardware. One jig is for measuring, and I have various holes drilled to wind longer or shorter skeins, and can add additional holes if I need much shorter strings, like say for a pistol crossbow. Making a string about 1" shorter than the distance between knocks is the rule of thumb to get the string at the 3.5" brace that is optimal for this prod, so since this prod comes in at 27.5" between nocks, I made the string 26.5" long. I do factor in some stretch, since I am using B-50 for this string, but is not so much of an issue that I make the string shorter to compensate. The 1" rule works out fine for me for this length of prod.
I wound on 40 winds, so this string has a breaking point of about 2000 lbs, I suspect more than enough for a 165 lb. pull

I did make it fatter than I needed to, just for aesthetic reasons, since a historicl string is a massive, massive thing, as big around as your thumb. And, frankly, having a way bit of extra insurance is not a bad thing. I did no doubt sacrifice some performance to a thicker string, but not enough to loose any sleep over.
Now, all wound up and ready to go, I put the skein on the stringing jig. Ugly, ain't it? I have the four steel rods there so I can serve the tips for half the width of the string, and then, after putting it on again after both ends are served, serve it again and have my loops. Then, I just serve the middle. Not all that much of the string itself is visible. The thing with crossbow strings is if you break one little fiber, the entire string is unservicable, so, all that serving serves a purpose.
Again, you are looking at the world's worst string maker, so forgive me.

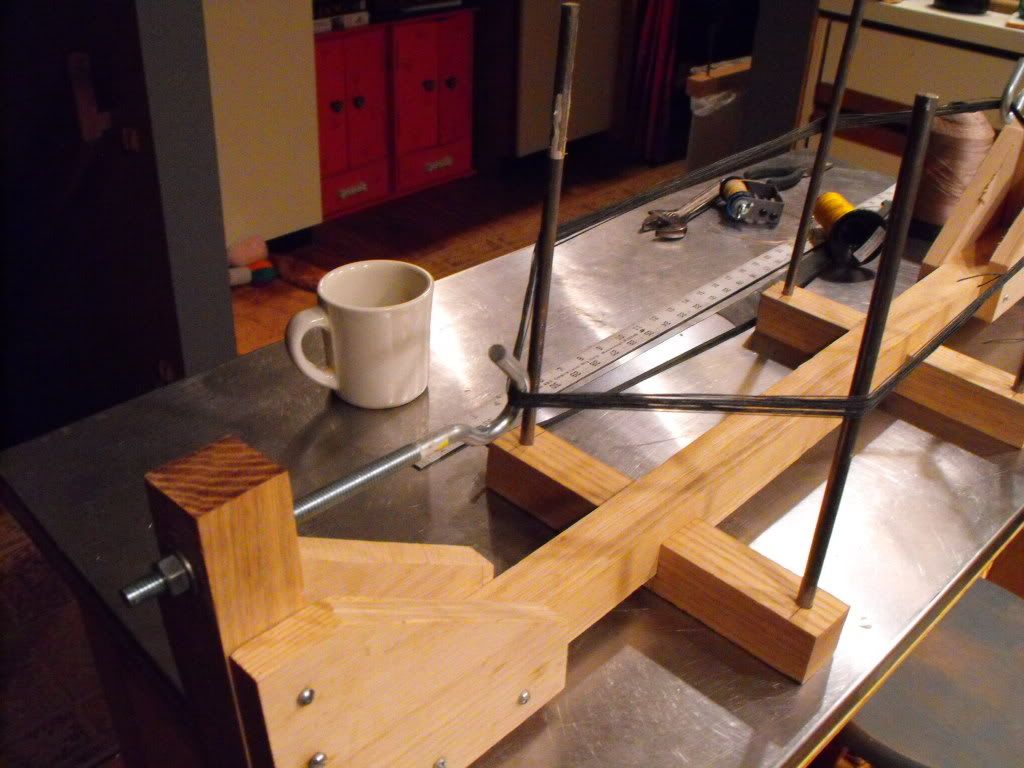
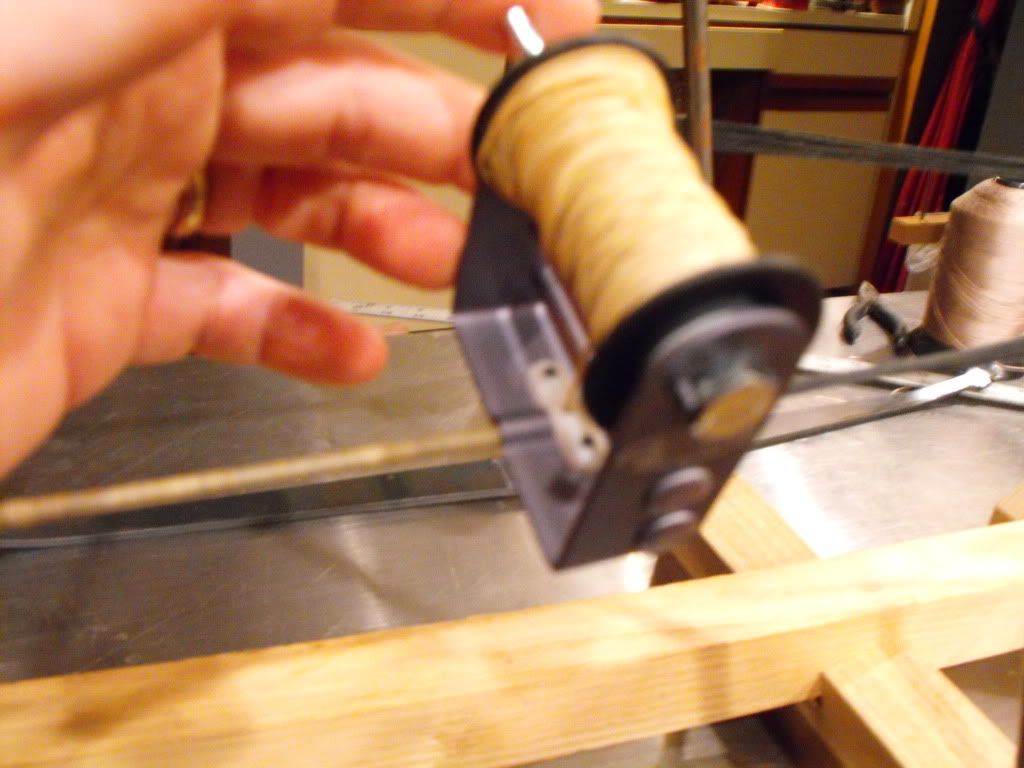
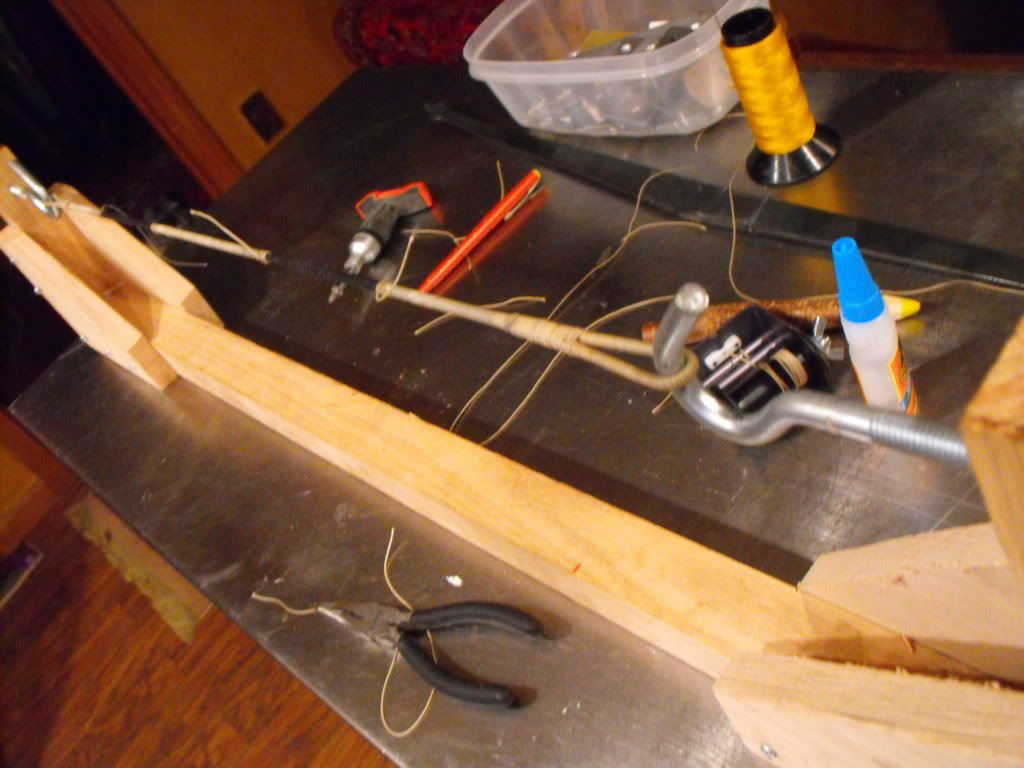
Last for now, I took care of getting that front ring on.
Yes, I heard someone in the back of the lecture hall ask why this is not hand forged? The answer is, I am not a smith. Since this is a first crossbow of this design, and since I am using stainless steel screws instead of rivets for the lock plate and front plating, I figured it would keep the entire weapons aesthetically pleasing, ie look nice. I love this style of crossbow, and expect to build a number of others, and then I can try out different ways of fabrication and different materials, including more authentic riveting, etc. Since though this is really in interpretation rather than a strict replica of a particular weapon, the stainless steel front ring I think is fine.
Now, the way I installed it and the way I probably should have installed it are entirely different. What I probably should have done is drill a hole a bit smaller than the outside diameter of the ring's shank, heated the shank up cherry red, and then installed it. Instead, I drilled a 3/8" hole the depth of the shank. There was quite a bit of play. I trimmed and wrapped the shank with a a very thin piece of buckskin, slathered it up with epoxy, and pounded the ring into its hole, while hoping the entire while the front of the tiller didn't split. Had that happened, you would have been woken up by my screams of horror and remorse.
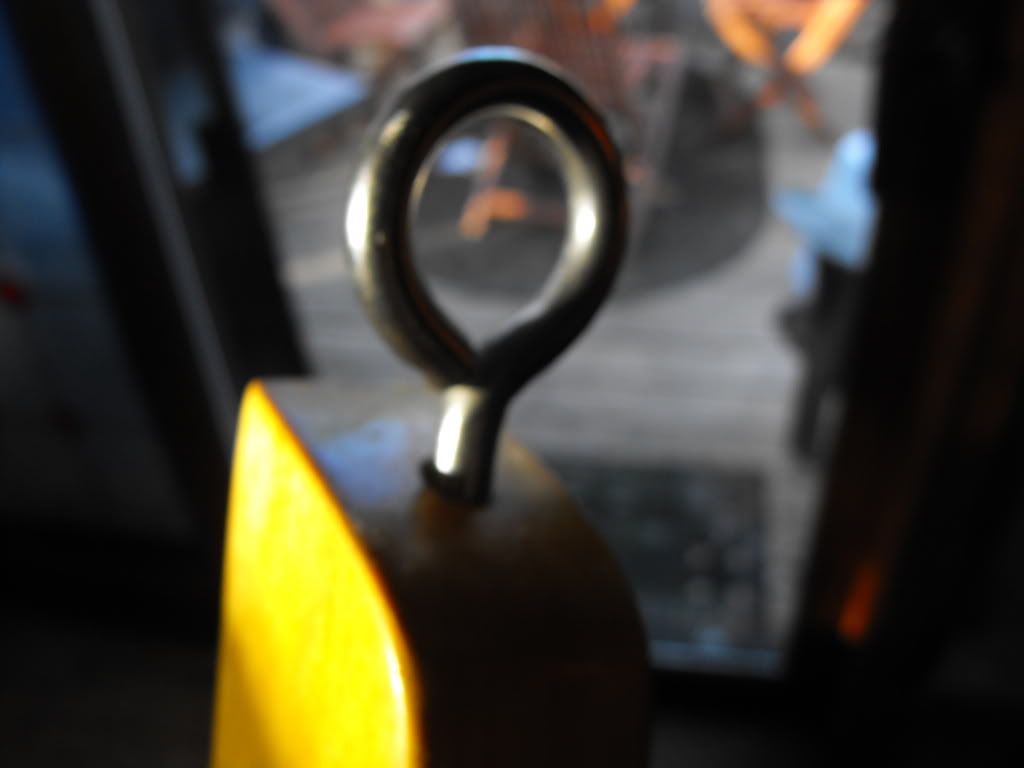
All went well, the tiller is still in once piece, and the ring is nice and snug in there. Whew. Oh, sorry about how fuzzy that photo is.
Later today, with a wee bit of luck, the crossbow will be essentially done. Stand by more more.
Dane