Since I had already bored holes in the tang, I will talk you through this one. With the guard seated firmly, I just lined the guard up with the front of the antler and marked and bored the holes. Normally, if the holes are not bored, I put the tang in the handle, and while holding it in tight, bore through the antler and against the steel just enough to mark a spot on the steel. Take the tang out, bore through the steel and put it back into the antler. Then bore back through the first hole, then in the steel and finally the antler on the other side. Insert a pins in the hole. This will hold everything in place while the second hole is being bored, insuring that the holes stay lined up. Now a word about pins. Inserting a blunt pin can be a pain, so I grind the tip down a little. It saves alot of cussing and time. These are not the pins I used, but they were handy for the picture.
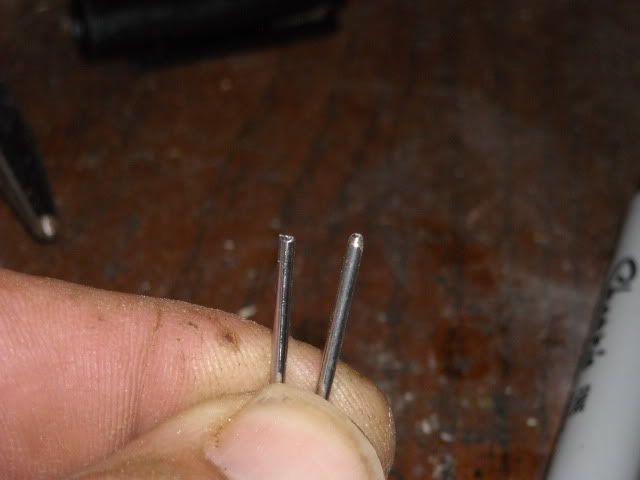
Here it is assembled and ready for some trim work on the guard. I know, somebody is saying that the pins are not straight. That happens. But, when they are cut off and ground smooth, nobody will notice.
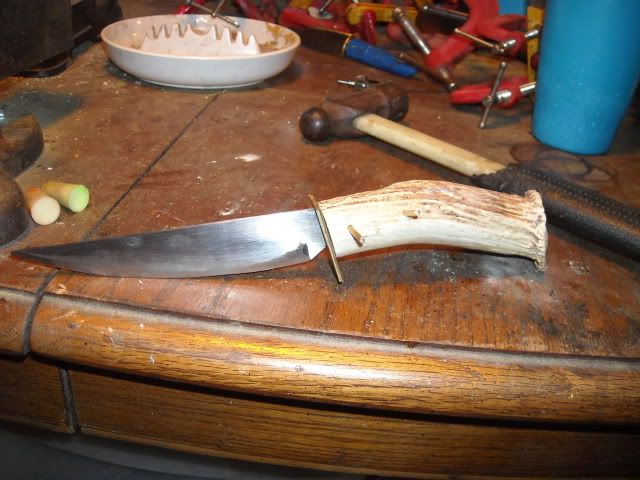
I marked the shape of the guard with a sharpie and removed it from the antler. I will do the shaping on the belt sander and don't want any sanding marks on the antler.
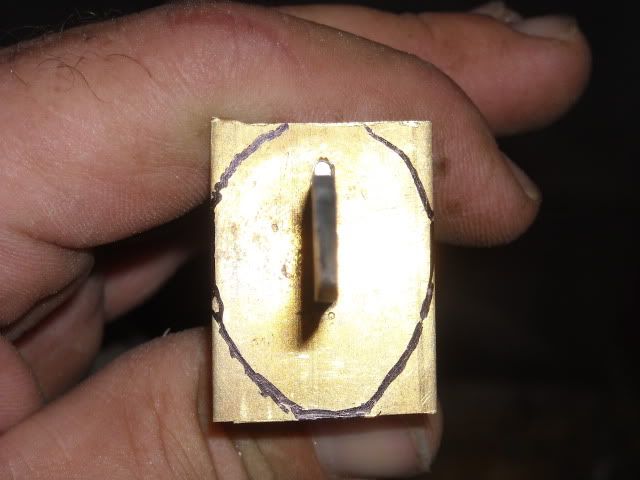
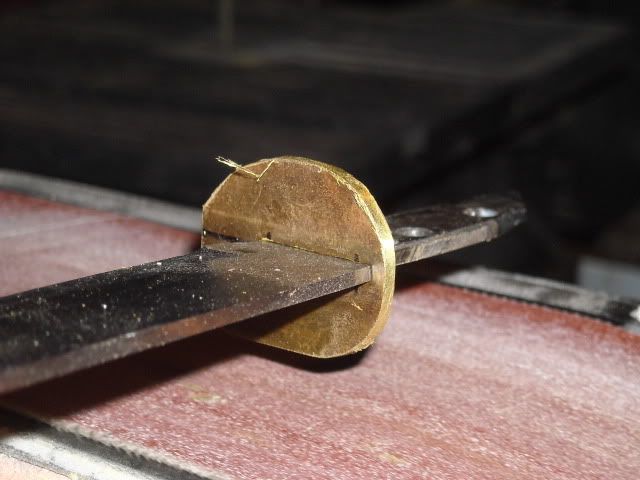
With that done, it is back to the buffing wheel for some shine. Notice how I am holding the blade against the wheel. If you get the back edge (where my pinky is) against the wheel, a 2000 rpm drill press can yank the blade out of your hands. Be careful. When one edge is polished, I flip the blade so that the point is up. That keeps the back edge away from the wheel. When one side is done, I work on the other side the same way. If the blade starts getting hot, quench it in water. Again, make sure you use the container that you have not been spitting in.
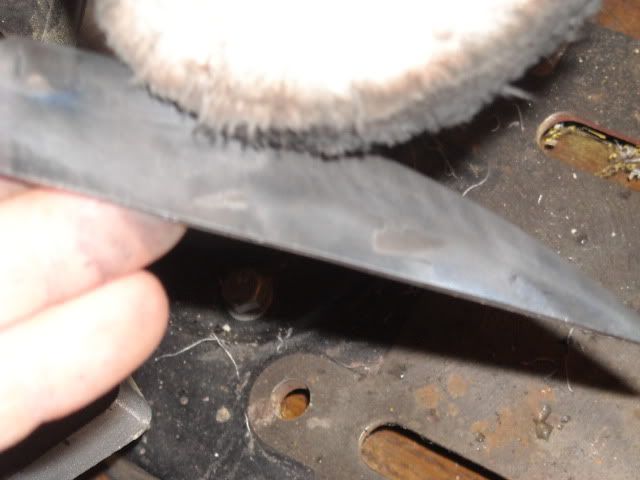
OK, the blade is fairly shiny and ready for assembly. I will shine it more when the epoxy dries. One of the reasons I only partially shine it is that there will be some of the epoxy ooze out around the guard. If you have spent the time shining it completely, you will scratch up the guard trying to get the epoxy off. I buff it to get it warm and the thin layer of epoxy will peel off the brass with minimal scratching.
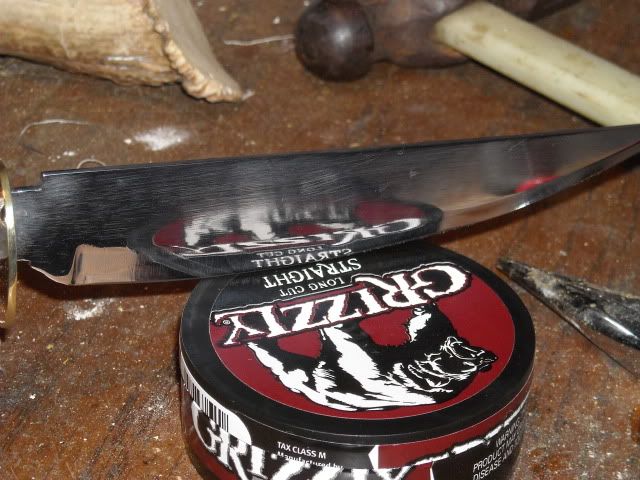
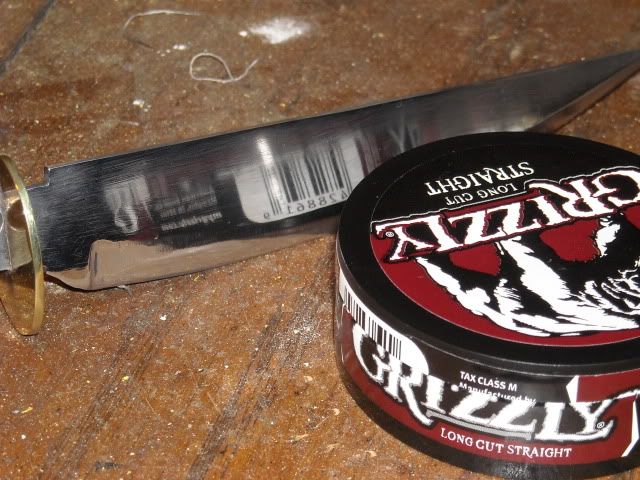
I use Devcon two part epoxy for most of my knives, mostly because of the holding strength. Mix enough to fill the hole. I use a small stick to probe around and get all the air bubbles out. It helps to wear some latex gloves while doing this. The stuff is sticky and does not want to wash off.
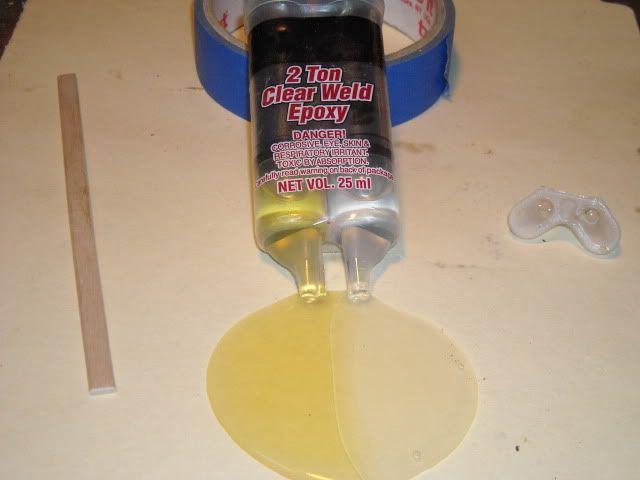
I tape the blade up completely and the antler. Then use one of the pins to pop holes in the tape where the pin holes are in the antler. This way you don't have to hunt for the holes while the antler in full of epoxy. Yes, some of the epoxy will ooze out of the pin holes, but things are about to get messy anyway.
Assembled, epoxied and ready to to press and dry.
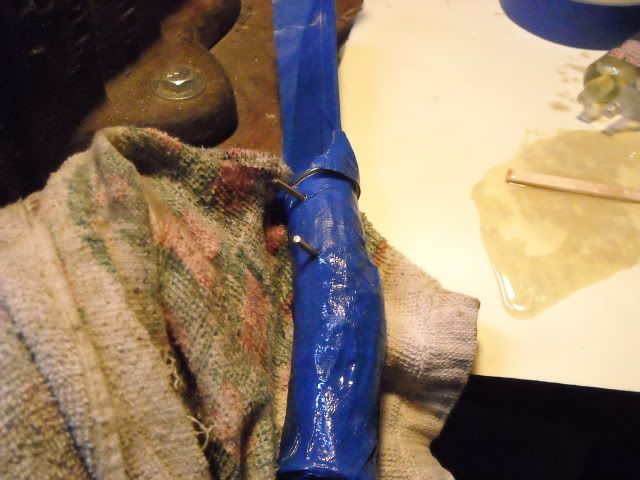
For the press part, I just use the vise and a piece of innertube. This will hold it in place while it dries. Things have a habit of shifting around some if they are not secured.
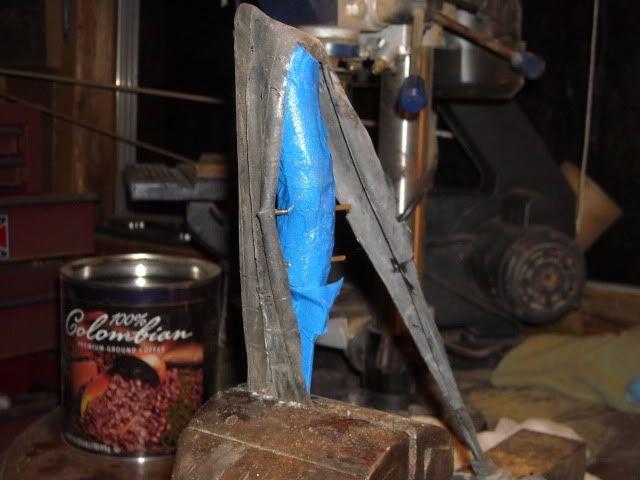